Dawna DąbrowaDzielniceCentrumKolejowa8
Dzielnice - Centrum - Kolejowa - 8
DEFUM, Fitzner i Gamper, Fabryka Zieleniewskiego, Fabryka Pełna Życia. Kilka nazw, jeden zakład. Niegdyś wiodąca fabryka przemysłu maszynowego w mieście, obecnie ma duże perspektywy stać się wiodącym obiektem kulturalnym miasta. Warto z tego powodu prześledzić jej historię.
Początki historii
Historia Dąbrowskiej Fabryki zaczyna się w latach 70-tych XIX wieku. Na miejscu zakładu działa wtedy warsztat ślusarski bliżej nieznanego przemysłowca. Na jego bazie w 1882 roku R. Farkac założył fabrykę. Być może to on był właścicielem wspomnianego warsztatu. Zakład od samego początku do końca swoich dni działał na potrzeby przemysłu maszynowego. Na samym początku pracował dla przemysłu cukierniczego, lecz prawdopodobnie wytwarzał jedynie elementy maszyn, a nie składał całe urządzenia. Kolejnym krokiem w historii zakładu było wykupienie go przez A. Braunsteina. W krótkim czasie, bo już 3 lata od założenia fabryki w 1885 dołączył do niego znany czeski przemysłowiec Emil Skoda (ten sam który zapoczątkował produkcję czeskich aut,a nadto w Pilznie tj miejscu urodzenia Emila Skody do dzisiaj funkcjonuje fabryka obrabiarek
o nazwie SKODA Machine Tool a s , o asortymencie produkcyjnym bardzo podobnym do asortymentu DEFUM). W latach 90-tych zakład znów zmienił właściciela-tym razem stali się nim przemysłowcy z Sosnowca- Wilhelm Fitzner oraz Konrad Gamper. W 1897 roku przekształcili DEFUM w „Towarzystwo Akcyjne Zakładów Kotlarskich i Mechanicznych W. Fitzner i K. Gamper”. Była to jedna z najbardziej znaczących spółek w Królestwie Polskim, posiadająca swoje oddziały w Warszawie, Łodzi i innych ważnych miast carskich. Jestto swoisty kamień milowy w historii zakładu, który zaważył na jego dalszych losach. Zmiany w formie przedsiębiorstwa skonkretyzowały produkcję dąbrowskiej fabryki na przemysł maszynowy.
Filia giganta
Niestety dąbrowski zakład był jedynie filią o wiele większego zakładu w Sosnowcu-mieści się on obecnie niedaleko Centrum Handlowego Plejada. W Dąbrowie siła zainstalowanych maszyn parowych wynosiła jedynie 100KM, podczas gdy w Sosnowcu była to liczba dziewięciokrotnie wyższa. Ten okres historii stwarza dość spore problemy, gdyż często w źródłach ciężko jest rozdzielić czy informacje dotyczą konkretnie dąbrowskiego zakładu czy ogółu Towarzystwa Fitznera i Gampera. Filia nosiła wówczas nazwę "Dąbrowska Fabryka Maszyn i Odlewnia Żeliwa". Jedna z największych reorganizacji zakładu miała miejsce w okolicy 1910 roku – w zasadzie większość historycznych budynków została wybudowana w tamtym czasie, w tym istniejąca do dziś hala montażowa i hala odlewni. Poza różnego rodzaju frezarkami i tokarkami, które były wymienianie na bieżąco, to większość parku technologicznego i narzędziowego zakładu do samego wybuchu wojny pochodziła właśnie z tych lat.Produkcja skupiała się na urządzeniach mechanicznych, - tokarkach, frezarkach, szlifierkach, gwinciarkach, wiertarko-frezarkach, strugarkach i tym podobnych maszynach. Zakład świadczył również usługi w zakresie odlewów żeliwnych, mosiężnych i brązowych o wadze do 30 ton i ich późniejszej obróbce. Dynamiczny rozwój fabryki zahamował wybuch I wojny światowej. Podczas okupacji fabryka produkowała na rzecz niemieckiego przemysłu, ale spora część maszyn została zdewastowana lub wywieziona. Po konflikcie fabryka zmagała się z problemem braku zamówień.W tym celu W. Fitzner i K. Gamper założyli Fabrykę Lokomotyw w Chrzanowie - znany dziś jako Fablok. Dzięki fabryce w Chrzanowie dąbrowska fabryka miała zapewniony zbyt produkcji, a kolej z racji odbudowy państwa i braku odpowiedniego taboru w nowo utworzonym państwie stawiała szerokie perspektywy rozwoju. Ponadto z inicjatywy dyrektora Jechalskiego rozpoczęto równocześnie produkcję seryjną obrabiarek. Mimo ww. zabiegów firma nadal zmagała się z trudnościami. By się im przeciwstawić, o Od 1928 roku DEFUM wszedł do spółki „Zjednoczone Fabryki Maszyn Kotłów i Wagonów L. Zieleniewski, Fitzner i Gamper S.A”. Od tamtej pory usystematyzowano produkcję jedynie w kierunku kotłów oraz obrabiarek. Co ciekawe niemal połowa produkcji obrabiarek w 1933 roku była produkowana na potrzeby wojska! A dokładniej dla Marynarki Wojennej, Państwowej Wytwórni Uzbrojenia oraz Państwowych Zakładów Inżynieryjnych.
Produkcja odbywała się w następujący sposób. Po otrzymaniu zamówienia biuro fabrykacyjne przygotowywało specjalne karty - operacyjne, na których opisywano przebieg obróbki poszczególnych elementów zamówienia, oraz karty robocizny i materiałowe. kierowało go do modelarni.Tam wytwarzano modele odlewnicze z drewna ,które służyły do wykonywania form odlewniczych w których odlewano różnego rodzaju korpusy maszyn i innych urządźen. Oczywiście DEFUM posiadał magazyn odlewów, więc w przypadku identycznych zamówień korzystano z poprzednich modeli. Odlewnia wytwarzała 4 podstawowe rodzaje żeliwa oraz dwa specjalne o podwyższonych parametrach. Ciekawostka - zakład ściągał koks z Czech, z okolic Karwiny zamiast korzystać z polskiego. Niestety nasz, ze względu na dużą kruchość nie nadawał się do zastosowania w odlewni maszynowej. Następnym etapem po odlewni była czyszczarnia. Z niej półprodukty trafiały do warsztatu mechanicznego, gdzie po przywiezieniu dodatkowych elementów z magazynu głównego składano maszyny. Dalej wędrowały one do ekspedycji która wysyłała elementy do zamawiającego. W przypadku samych odlewów oczywiście omijano warsztat mechaniczny. Transport po terenie fabryki odbywał się po torach wąskotorowych, a do celów pociągowych używano wyłącznie koni. Zakład posiadał również bocznicę normalnotorową. Park maszynowy był bardzo różnorodny i rozbudowany. Najstarsze tokarki pochodziły w okresie międzywojennym pochodziły nawet z 1895 roku. Moc zainstalowana w zakładzie w 1933 roku wynosiła 140 KM w maszynach parowych i ponad 900 KM w silnikach elektrycznych.
W 1934 roku planowano w zakładzie otworzyć małe laboratorium na potrzeby odlewni metali. Z ciekawostek można podać iż np. w roku 1937 koszty produkcji wyniosły 1,8 mln ówczesnych złotych, w tym 1,1 mln przeznaczono na zakup materiałów, 330 tys. na pensje robotników, a 130 tys. na pensje urzędników. Dla porównania cena bochenka w tamtych latach to około 30 groszy. Krótko przed II wojną światową zakład przyjął nazwę Babock-Zieleniewski.
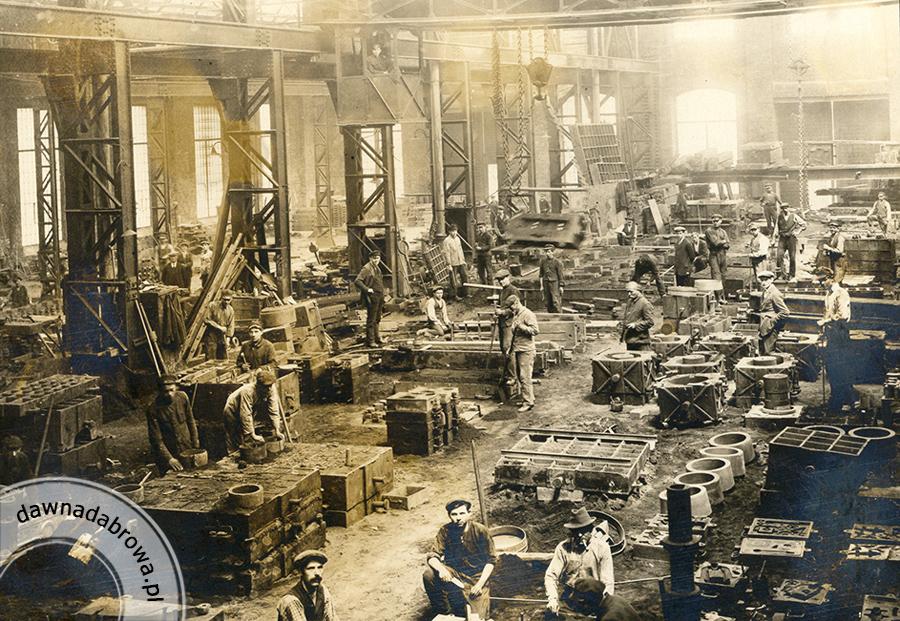
Fot. 1 Hala DEFUM w latach międzywojennych
II wojna światowa
Zakład przeszedł pod zarząd Trebsngeselsch Ost G.N.. W maju 1941 roku zakład został nabyty przez AG Ferrum. Zakład przez długi okres czasu produkował urządzenia na rzecz niemieckiej machiny wojennej. Produkcja została znacząco zitensyfikowana w stosunku do międzywojennej sytuacji - zatrudniano ponad 1000 pracowników i pracowano na trzy zmiany. Odlewnia została przeniesiona do Zabrza, a dotychczasowe pomieszczenia zajęła kolejna hala montażowa. Następne informacje są sprzeczne - jedne źródła podają że zakład został opuszczony przez okupanta zdewastowany, inne że wogóle nie zdążyli ruszyć ani jednej maszyny. W każdym razie Defum wrócił do pracy jeszcze w styczniu 1945 roku – przy czym trzeba wspomnieć iż Niemcy zostali wyparci z Dąbrowy dopiero 27 stycznia. Z polecenia Rady Zakładowej, kierownictwo powierzono inżynierowi Tadeuszowi Furdynowi. W marcu 1945 roku zakład przekazał Departamentowi Uzbrojenia 10 nowych obrabiarek. Ściągnięto również z powrotem odlewnię z Zabrza. Oprócz produkcji obrabiarek, zakład wykonywał również naprawy i remonty czołgów na potrzeby Ludowego Wojska Polskiego.
Złota era PRL-u
W czasach PRL DEFUM został upaństwowiony – dokładnie 30 listopada 1949 roku. Była to jedynie formalność, a zakład pracował dla państwa od samego końca wojny. Wraz ze zmianami własnościowymi przyszła zmiana nazwy na „Śląsko-Dąbrowska Fabryka Urządzeń Mechanicznych im. Stanisława Krzynówka”.2 lutego 1946 roku wyprodukowano setną obrabiarkę po II wojnie, a w listopadzie 1948 500-tnej. Oczywiście regularnie wykonywano plany wieloletnie, tak jak w każdym polskim zakładzie w tamtych latach. W 1950 roku wyprodukowano 35 tokarek-karuzelówek i 80 wiertarko-frezarek. W 1965 roku wyprodukowano 41 tokarek karuzelówek i 211 wiertarko-frezarek. Krótko po tym wydarzeniu rozszerzono asortyment produkcji o tokarki karuzelowe. W 1962 roku przyłączono do niego Szopienicką Fabrykę Obrabiarek.1964 rok przyniósł zmiany technologiczne. Przestarzałe modele obrabiarek CWC i HWC zostały zastąpione przez WFA-80 i WFA-100.
Kolejne zmiany organizacyjne przyszły w 1970. Na bazie czterech fabryk tj. FUM PORĘBA , DFO-DEFUM , Bielskiej Fabryki Obrabiarek oraz Jędrzejowskich Zakładów Mechanicznych został utworzony Kombinat Obrabiarek Ciężkich PONAR-PORUM . W 1975 nastąpiła nowa próba
integracji i tym razem utworzono Kombinat Obrabiarek Cięzkich PONAR-ZAWIERCIE który obejmował trzy fabryki tj. FUM-PORĘBA ,FO-RAFAMET i DFO-DEFUM . Żadna z tych koncepcji integracji nie zyskała jednak szerokiego poparcia poszczególnych zakładów i około roku 1980 powrócono do wcześniejszej samodzielności poszczególnych fabryk . Każda z fabryk
miała inną specjalizacje produkcyjną i każda z nich była uznanym producentem i eksporterem
swoich obrabiarek . Produkcja obrabiarek ciężkich w latach PRL-u była uznana za polską specjalność eksportową, a próby integracji tych znanych w świecie fabryk kończyły się rywalizacją o prym w połączonym kombinacie, co szczególnie było widoczne pomiędzy PORĘBĄ a RAFAMETEM.
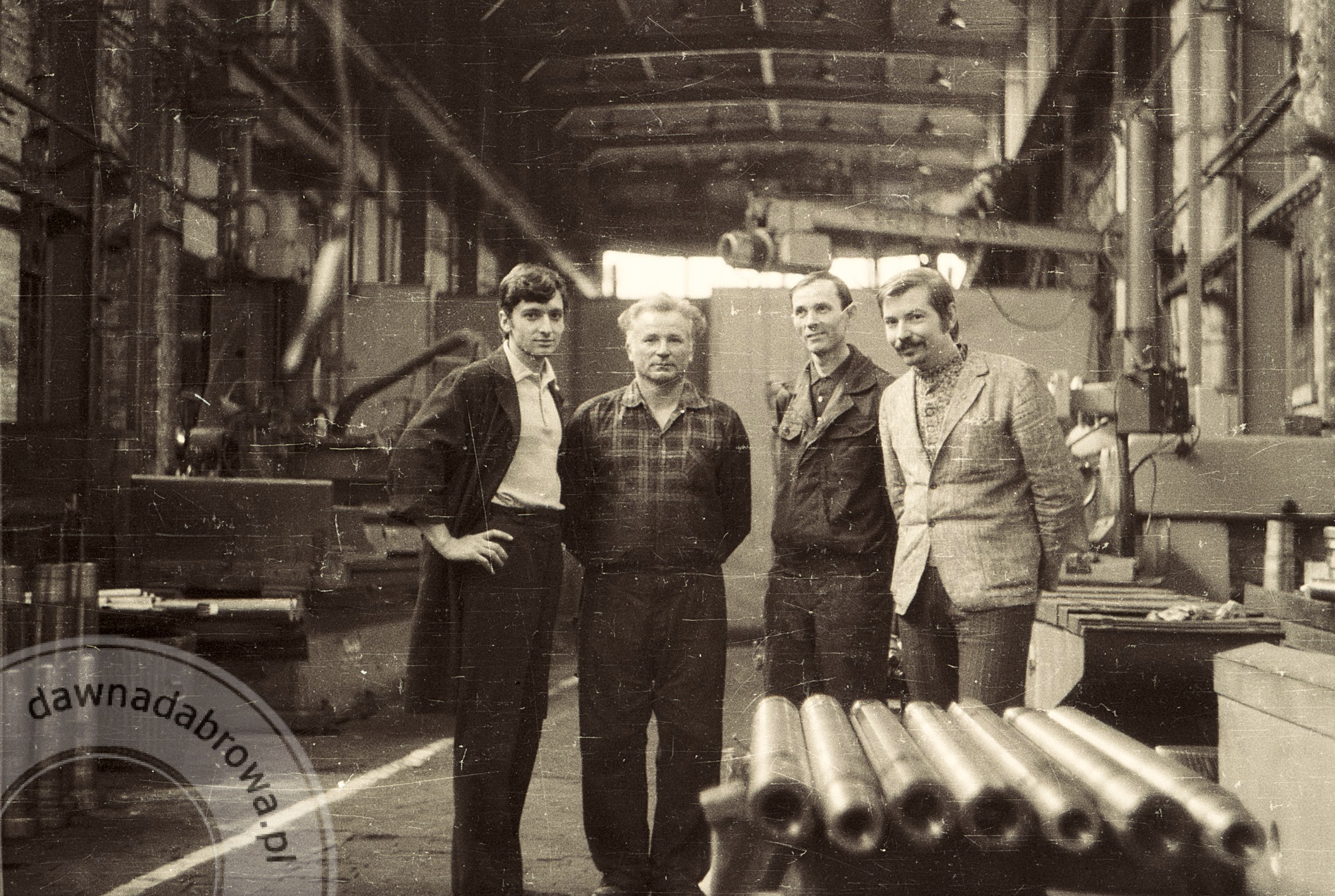
Fot.2 Zdjęcie hali produkcyjnej i pracowników, lata PRL-u
Obrabiarki, obrabiarki, obrabiarki...
Lata 70-te XX w to okres odbudowy przemysłu na całym świecie po zniszczeniach wojennych. Skutkuje to ogólnoświatową koniunkturą dla producentów dóbr inwestycyjnych dla przemysłu i w tym znacznym popytem na obrabiarki DEFUM.
Produkowane są wiertarko – frezarek i tokarki karuzelowe konwencjonalne a także początkowe serie obrabiarek sterowanych numerycznie z układami sterowania General Electric i Nucon -Asea. Okło 80 % produkcji jest eksportowane. W przedziale lat 1970 – 1975 eksport fabryki do krajów
zachodnich wzrósł o ok. 300 % Z fabryki wychodzą całe składy kolejowe wysyłane głównie do portu w Gdyni i dalej do krajów docelowych obu Ameryk a nawet Australii . Równolegle odbywa się dystrybucja drogą lądową do krajów Europy Zachodniej . Krajowi inwestorzy maja trudności w zakupie obrabiarek DEFUM gdyż eksport traktowany jest priorytetowo z uwagi na zarabianie niezbędnych dla kraju dewiz . W każdym miesiącu z fabryki wychodzi od 20-tu do 40-tu obrabiarek. W chwili uruchomienia produkcji każda obrabiarka ma już swojego docelowego odbiorcę .
Lata 70-te XX w obejmują produkcje n/w typów obrabiarek:
Wiertarko-frezarki WFM-100.
Lata 80-te i 90-te XX w to całkowite przejście do produkcji obrabiarek sterowanych numerycznie.
Powstają zupełnie nowe konstrukcje,stale doskonalone i modernizowane . Asortyment produkcyjny zostaje zawężony do wydajnych i konkurencyjnych obrabiarek wyposażanych w sterowania numeryczne SIEMENS, HEIDENHAIN i FANUC .
W tym okresie produkowane są:
Zakład posiadał dwa loga – stworzone w PRL składało się z niebieskiego koła, którego obwódkę górnej części stanowiło koło zębate, a dolnej wieniec laurowy. W koło była wpisana kursywą i podkreślona nazwa zakładu – „Defum”. Drugim logiem zakładu były trzy litery „DFO” zamknięte w kole zębatym.
Pomieszczenia fabryczne
Defum to ogromny zakład składający się z tysięcy pomieszczeń, hal, magazynów, poddaszy. Opisanie każdego najdrobniejszego szczegółu zajmie bardzo dużo czasu i będzie stopniowo rosło z czasem. W celu dokładniejszego poznania zakładu ponumerowałem wszystkie budynki na mapce.
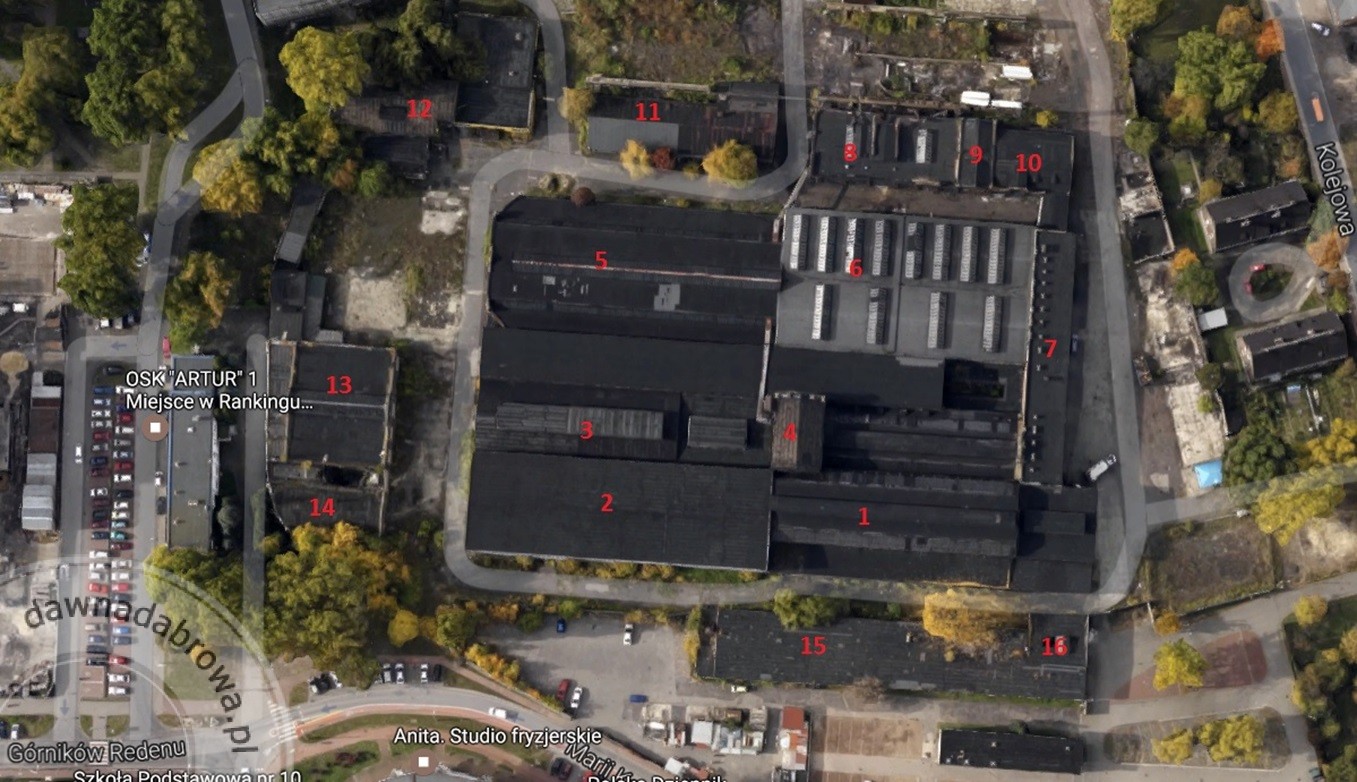
Główny człon zakładu stanowi zespół hal fabrycznych ponumerowanych od 1 do 6. W okresie międzywojennym wyróżniały się na tle pozostałych zakładów w okolicy. Były bardzo przestronne, doskonale oświetlone, wentylowane i zelektryfikowane. Zostały utrzymane w secesyjnym stylu
Hala numer 1
Hala ta pochodzi z okresu międzywojennego. Zastąpiła wcześniejszą halę z XIX wieku. Wykonana została w technice stalowo-ceglanej w kształcie odwróconej litery „T” w stylu modernizmu. Główny środkowy trzon stanowił trapezoidalny, oszklony dach, a po obu bokach symetrycznie ciągnęły się niższe partie hali. Pomiędzy cegły umieszczono żelazne pręty wzmacniające konstrukcję. Jej wschodnia oraz północna ściana zostały zachowane względnie oryginalnym stanie. Sama konstrukcja nie została zmieniona, wymieniono jedynie szkło na materiał z tworzywa sztucznego i dodano PRL-owskie instalacje techniczne. Północna fasada hali była pozbawiona ozdób architektonicznych – jedynym ciekawym elementem było ogromne przeszklone okno. Z tej strony do zakładu dochodziła bocznica kolejowa, która przez bramę mogła wjechać do wewnątrz hali. Wschodnia część hali składa się z ciągnących przez całą długość okien oraz ozdobnego grzymsu pod linią dachu. Niegdyś hala była o wiele dłuższa i kończyła się mniej więcej w miejscu dzisiejszej hali nr 2, jednak w PRL ściany tej części zostały wyburzone. Możemy się jednak domyślać iż była utrzymana w identycznym stylu architektonicznym. Od zachodniej strony przylega W środku hala nr 1 prezentuje się naprawdę okazale. Co kilka metrów stoją ogromne, kilkumetrowe secesyjne żelazne słupy podtrzymujące konstrukcję dachu. Warto zwrócić uwagę na ich nitowanie. Górny, trapezoidalny dach był utrzymany przez przepiękny, stalowy szkielet na którym były umieszczone przemysłowe lampy. Konstrukcja dachu była drewniana. Większość przestrzeni nie była podzielona żadnymi ściankami działowymi i stanowiła jeden kompleks. Jedynie po wschodniej stronie znajdowało się jedno piętrowe pomieszczenie socjalne (dziś już praktycznie wyburzone) oraz zabudowana transformatorownia – obecnie wybebeszona, prawdopodobnie zostanie wyburzona.. Co ciekawe na dachu tej hali znajduje się WPO- Wieżowy Punkt Obserwacyjny, system obrony przeciwlotniczej z okresy lat 50-tych.
W hali znajdowała się odlewnia żeliwa, która wykonywała odlewy na potrzeby produkowanych w DEFUM maszyn. Do przygotowanych w innych budynkach modeli wlewano ciekły metal. W PRL była podzielona na dwie części. Jedną z nich była karniarnia - to część wydziału gdzie wykonywało się rdzenie formierskie. Kranistą nazywano - suwnicowego, który „jeździł kranem” co dziś może brzmieć trochę zabawnie. Jak łatwo się domyślić była to osoba odpowiedzialna za wlewanie materiału do form.
Kastlami nazywano skrzynie formierskie, a giserami formierzy. W 1974 roku zlikwidowano starą odlewnię, a halę zaadaptowano na dział obróbki mechanicznej i cieplnej.
Hala nr 2
Historia hali jest bezpośrednio połączona z halą nr 1, gdyż do PRL-owskiej przebudowy stanowiły jedną integralną część. W późniejszych latach wyburzono boczne ściany, zachowując jedynie samą konstrukcję oraz dach. Ściany zostały podwyższone do jednolicie wysokiego prostokątnego kształtu i obłożone blachą falistą. Również w ten sam sposób zabudowano okna dachowe, pzostawiając jedynie dwa wąskie pasy okien na bocznej ścianie.
Hala nr 3
Jest to kolejna historyczna hala która prawdopodobnie powstała wraz z pozostałymi zabudowaniami. Przyklejona jest do zachodniej ściany hali nr 1 Niegdyś stała wraz z nią osobno i nie była przyklejona do innych zabudowań. Jednak w wyniku przebudowy fabryki zachodnia i południowa ściana stały się niejako ściankami działowymi większego kompleksu. Nie zostały na szczęście wyburzone, poza wyjątkiem w miejscu bramy między halami, a jedynie zamurowane.
Za ściany zaadaptowano zewnętrzne fasady historycznych hal. Nie zostały one wyburzone, a jedynie za- i nad-budowane. Dzięki temu w przyszłości będziemy mogli wrócić do pierwotnego stanu. W środku znajdowała się wydzielona siatką przestrzeń oraz umieszczone na wysokości pierwszego piętra warsztaty. Powyżej opisane pomieszczenia dodatkowe są z duża dozą pewności wytworem PRL-u – w oryginalnym projekcie hala nie była przedzielona żadnymi dodatkowymi pomieszczeniami. Wyjątek stanowi wiszący nad halą magazyn w południowo-zachodnim rogu hali nr 1. Jest to pomieszczenie znajdujące się pod wieżą wodną zakładu opisanej w punkcie 4.
Wieża wodna 4
Wieża wodna istnieje od samego początku zakładu. Jest niejako wklejona w halę fabryczną. Na poziomie gruntu w niczym pod wieżą znajduje się po prostu pusta przestrzeń hali. W zachodnim rogu znajduje się metalowa klatka schodowa prowadząca na wyższe kondygnacje. Na wysokości pierwszego piętra znajduje się „wiszące” pomieszczenie magazynowe. Z niego wchodzimy schodami do górnej części – właściwej wieży wodnej. Dziś jest to puste pomieszczenie, lecz kiedyś mieściło ono nitowany, metalowy zbiornik wody używanej do procesów technologicznych. Wraz z przyłączeniem DEFUM do sieci wodociągowej przestała mieć znaczenie i prawdopodobnie została zmieniona w magazyn.
Hala nr 5
Ten budynek był głównym sercem zakładu. To tutaj znajdowała się montownia maszyn mechanicznych. Jednocześnie był to najbardziej bogaty w detale budynek fabryki. Głównym elementem architektonicznych bocznych fasad były ceglane pilastry dzielące go na segmentu. Pomiędzy nimi znajdowały się półkoliste, przestronne okna. Każde z nich posiadało bogaty zdobione nadproże, i szereg grzymsów. Frontowa fasada hali, od strony południowej składała się z osi czterech kolumn – dwóch bocznych i dwóch środkowych. Ich szczyty zostały zwieńczone okręgami i frezami. Między środkowymi kolumnami umiejscowiono trójkątny szczyt u góry, a pod spodem przestronne okno z ozdobnym nadprożem ze zwornikiem. Po obu stronach symetrycznie znajdowały się bramy do zakładu, dziś zamurowane. Możliwe że w czasach przedwojennych w półkolu umieszczonym na środku fasady znajdowało się logo zakładu. W środku hali znajdziemy również wspaniałe, secesyjne żelazne słupy oraz stalowy szkielet konstrukcyjny drewnianego dachu. Jej zachodnia strona została w PRL-u zabudowana piętrowymi warsztatami, ale pozostała część gmachu stanowi jedną całość nie przedzieloną żadnymi ściankami działowymi.
Hala nr 6
Budynek początkowo stanowił jedność z halą nr 5. Przebudowie uległy ściany zewnętrzne które zostały znacząco podwyższone, oraz dach. Część żelaznych słupów wewnątrz pochodzi z pierwotnej, XIX wiecznej hali. Nie wiem niestety czy przebudowa została wykonana jeszcze przed wojną czy już w czasach PRL-u.
Biurowiec nr 7
Budynek powstał we wczesnych latach PRL-u, zastąpił pierwotny budynek dyrekcyjny mieszczący się po prawej stronie bramy wjazdowej, dziś już wyburzony. Biurowiec posiada połączenie z halami produkcyjnymi na parterze(przez portiernię) oraz na piętrze(przez szatnię). W środku znajdziemy symetryczny układ jednakowych biur po obu stronach korytarza i zwyczajną klatkę schodową. Warto jednak zwrócić uwagę na interesujące, prostokątne balustrady. Wewnątrz biurowca znajdowały się biura zarządu, punkt wymiany i reperacji odzieży, dział produkcji, kasa, portiernia, archiwum, powielarnia dokumentacji, dział kadr i organizacji pracy, centrala telefoniczna, dział marketingu i handlu, dział techniczny TKT, sekretariat, biuro dyrektora naczelnego i jego zastępcy, dyrektora produkcyjnego i jego zastępcy.
Kotłownia nr 8
Budynek powstał w 1910 roku. Składa się z dwóch symetrycznych i identycznych członów. Pierwotnie, przed wojną tylko część południowa stanowiła kotłownię, a druga halę maszyn. W PRL połączono je w jedną funkcję kotłowni. Fasadę stanowią cztery kolumny, między którymi umieszczono trzy przestronne okna z nadprożami połączonymi zwornikiem. W środkowej części tuż pod linią dachu w okręgu umieszczono datę budowy. W środku znajdują się dwa kotły ciepłownicze i szereg pomieszczeń technicznych. Dach prawdopodobnie został przebudowany w PRL-u.
Budynki techniczne nr 9,10,11, 12
Wszystkie budynki pochodzą sprzed II wojny światowej. Ich fasady wykonano w podobnym stylu do reszty budynków. Zobaczymy tu ozdobione ceglanymi nadprożami okna oraz gzymsy między kondygnacjami. Przed wojną budynek nr 9 pełnił funkcję łaźni, numer 10 wozowni, stajni oraz kasyna. W PRL mieścił się tam skład obrony cywilnej, warsztat napraw(parter) i magazyn części elektrycznych(na piętrze). Budynek nr 11 to magazyn fabryczny. W PRL zorganizowano w środku dział obróbki cieplnej, do dziś można zobaczyć pozostałości pieców oraz kadzi. Budynek nr 12 to skład modeli na potrzeby odlewni, funkcję te zachował od czasów międzywojennych do końca PRL-u. W środku znajduje się niewielka suwnica, klatka schodowa i pomieszczenia magazynowe. Wokół niego znajdowały się budynki wybudowane w PRL-u – m.in. skład chemikaliów.
Budynki techniczne nr 13,14,15,16
Budynek nr 13 to czyszczarnia wybudowana w 1912 roku. W środku czyszczono wykonane w odlewni części do maszyn. Budynek numer 14 przed wojną mieścił składnicę odlewni, w PRL zmieniono jego funkcję ( niestety nie znaną mi). W okresie przedwojennym w budynku nr 15 znajdował się magazyn główny, ekspedycja oraz sprężarnia. W latach 60-tych budynek został znacząco przebudowany, możliwe że został wyburzony do fundamentów. Na jego miejsce powstała narzędziownia. Parter zajmowała długa hala posiadająca niegdyś niewielką suwnicę. Na piętrze znajdowały się biura-tak jak wskazują tabliczki na drzwiach sekcja technologiczna, zakupu narzędzi, wynalazczości. Budynek nr 16 to przedwojenna kuźnia, praktycznie w stanie ruiny. Warto w tym miejscu wspomnieć jeszcze o znajdującej się między halami niewielkiej remizie strażackiej.
W latach PRL-u w DEFUM działały cztery oddziały: obróbki mechanicznej, mechanicznej ciężkiej, mechanicznej lekkiej oraz montażu. W 1966 roku na zakładzie wybudowano nową hale montażową wraz z zapleczem socjalnym. W latach 1969-71 wybudowano nowoczesny biurowiec który pomieścił biuro konstrukcyjne. W tym samym czasie przeprowadzono remont głównej hali montażowej. Co najmniej od 1972 do 1976 roku zakład posiadał własną, 3-letnią szkołę zawodową, która mieściła się w budynkach dzisiejszego ZST oraz orkiestrę dętą. Pojawiają się również relacje o szkole zawodowej działającej w latach 1945-1950 w prywatnym budynku na ulicy Bolesława Limanowskiego.
Kadry i społeczność
Bardzo ważnym elementem zakładu były kadry i ich doskonała współpraca. Dzięki niej i odpowiedniemu podejściu kierownictwa do zwykłych pracowników zakład odnosił sukcesy. W roku 1913 fabryka zatrudniała 376 robotników i 55 urzędników. Nie zatrudniano wtedy kobiet, choć w latach 1900-1913 aż 5% załogi stanowili młodociani przed 18 rokiem życia.
Wraz z nadejściem ery PRL-u w fabryce rozwinęło się zaplecze socjalne. Pojawiły się domy fabryczne, wczasy pracownicze, ambulatorium, świetlica zakładowa. Wprowadzono bezpłatną odzież roboczą, zaczęto szkolenia pracowników w technikum w Bytomiu. W późniejszym okresie zakład otworzył własną szkołę na ulicy Bolesława Limanowskiego, opisaną w oddzielnym rozdziale. W fabryce utworzyły się koła Towarzystwa Przyjaźni Polsko-Radzieckiej, Liga Kobiet, Koło Wynalazców.
Kolejni dyrektorzy:
W okresie ok. 1890-1914 struktura zarządu przestawiała się następująco:
ZNACZĄCE OSOBY KADRY TECHNICZNEJ I KIEROWNICZEJ PO 1945 ROKU
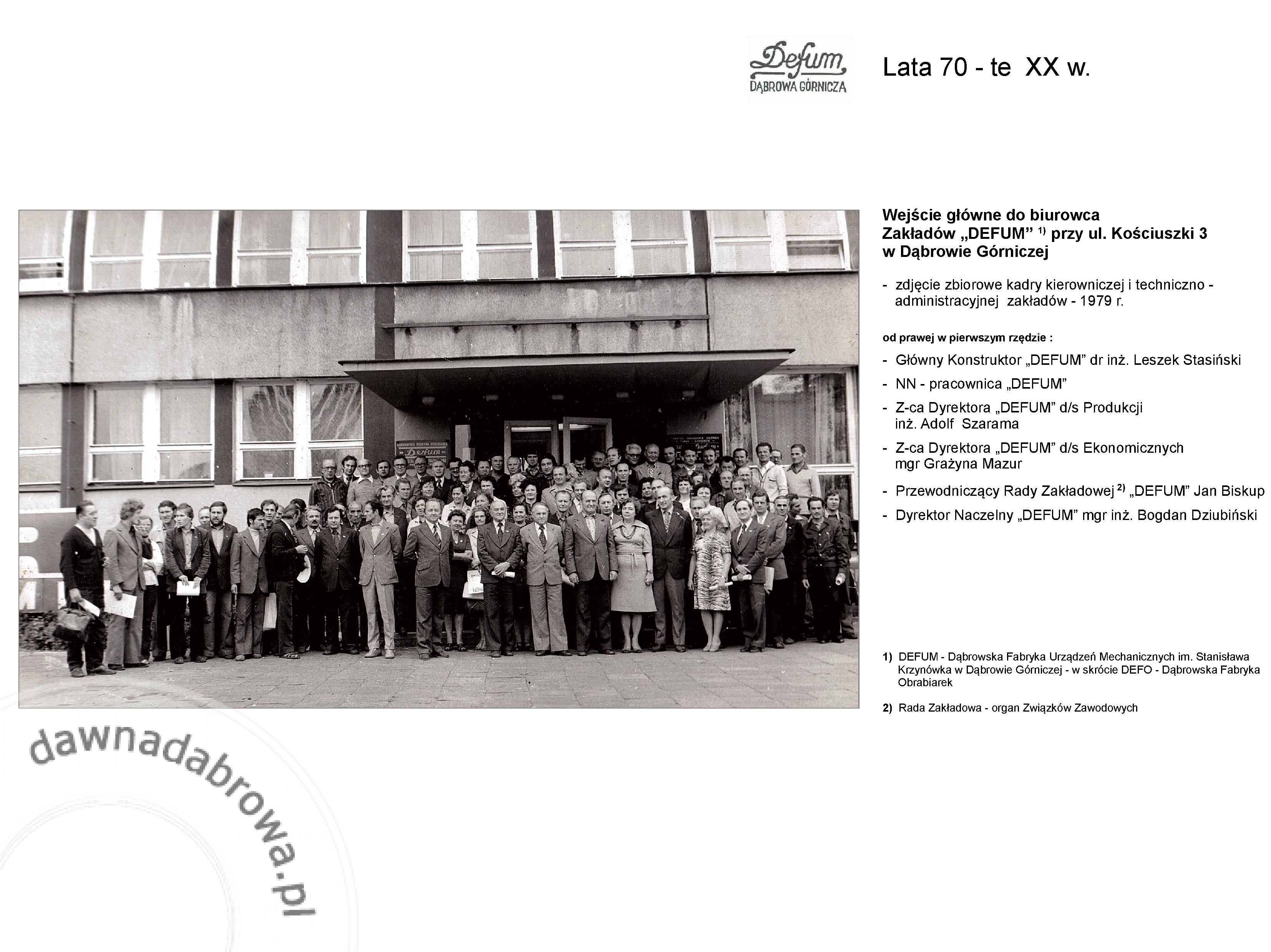
Pracownicy Defum obchodzili Dzień Metalowca. Wydarzenie uświetniała gala na deskach Pałacu Kultury Zagłębia.
W 2003 roku pracowało 300 osób, w 2010 110 pracowników a w 2011 80.
Zarządcy komisaryczni i likwidatorzy w okresie 2000 do 2015 roku:
Wojciech Miszczyk ,Mirosław Urbańczyk, Roman Sowiński , Wiesław Kaczmarski, Małgorzata Haładyj ,Anna Michałek ,Barbara Szkoda ,Jacek Wanic, Krzysztof Wrona (likwidator od 2013)
Statystyki Produkcji:
1933 rok - 20 obrabiarek, 600 ton odlewów i armatury
1937 rok - 77 obrabiarek, 1210 ton odlewów i armatury, zużywając 2000 ton surowców metalowych i 1200 ton paliwa w postaci węgla i drewna
1977 r. -165 obrabiarek, z czego 120
maszyn wyeksportowano do krajów zachodnich – głównie:
Włochy, Anglia, RFN, Turcja, Syria, Argentyna, USA
W podziale na typy:
– wiertarko-frezarki – WFB-80 33 szt.
– wiertarko-frezarki – WHB-150 4 szt.
– wiertarko-frezarki-ADS-115 12 szt.
– wiertarko-frezarki – ADP-115 6 szt.
– wiertarko-frezarki – HWCS-110 2 szt.
– tokarki karuzelowe – KNA-110/135 A 40 szt.
– tokarki karuzelowe – KNA-110/135 A (wersja amerykańska)..14 szt.
– stoły obrotowe – S-1600 9 szt.
Szkoła pracownicza
DEFUM posiadało własną szkołę pracowniczą.
Początkowo przed wojną nowi pracownicy szkolili się odbywając 4 letnią, słabo płatną praktykę zakończoną otrzymaniem zaświadczenia.
W erze PRL-u na samym początku wysyłano pracowników na przeszkolenie do Technikum w Bytomiu. Potem jednak utworzono własną szkołę przy ulicy Bolesława Limanowskiego 24. Otwarto ją 3 września 1946 roku. Pierwszym dyrektorem został Mieczysław Skarbek. Na początku szkoła posiadała 110 uczniów w dwóch klasach pierwszych i w jednej drugiej.
Rok szkolny 1947/48 przyniósł dwie klasy pierwsze, dwie klasy drugie i jedną trzecią przy licznie 178 uczniów. Od początku roku szkolnego dyrektorem był Józef Kwiatkowski, a od kwietnia Tadeusz Rączka. Wtedy też zaczęły się pierwsze egzaminy czeladnicze które ukończyło 22 uczniów.
W roku 1948/49 dyrektorem został Mikołaj Orłowski a liczba uczniów wyniosła 228 osób. Trzy dni nauki odbywały się w szkole, w prywatnym, nieprzystosowanym budynku, a kolejne trzy dni w warsztatach szkolnych na terenie fabryki - dziś już nie istniejące - stały w miejscu dawnego targowiska, dziś parkingu WSB. Personel nauczycieli składał się z 12 osób, z czego 7 osób to byli nauczyciele zawodu a reszta dochodząca.
W późniejszym okresie, w latach 70-tych szkoła przeniosła się na ulicę Łańcuckiego, do obecnego pawilonu "B" Technicznych Zakładów Naukowych. Jej pełna nazwa wówczas brzmiała "Technikum dla pracujących Dąbrowskiej Fabryki Obrabiarek Defum , Huty im F. Dzierżyńskiego i Huty Katowice". Zajęcia odbywały się w godzinach popołudniowych i wieczornych, a klasy były podzielone na "huciane" i "defumowskie". Program nauczania był dość spójny z resztą techników w Polsce, lecz nauczyciele mieli możliwość lekkich modyfikacji treści wskazanych dla danego zakładu pracy przy przedmiotach zawodowych. W klasach defumowskich były wprowadzone elementy budowy i programowania obrabiarek sterowanych numerycznie. Wśród nauczycieli znalazły się takie osoby jak Tomasz Derda, Tadeusz Białas , Zdzisław Flak, Jan Wiaderek, Helena Wiaderek. W tym samym budynku w godzinach dopołudniowych działa Zasadnicza Szkoła Zawodowa sponsorowana prze te same fabryki. Szkoła współpracowała z warsztatami szkolnymi DEFUM które posiadały własną hale , a także wyposażenie maszynowe niezbędne do szkolenia uczniów w zawodzie tokarzy ,frezerów, ślusarzy i w innych zawodach przemysłowych. Uczniowie którzy odbywali praktyczna naukę zawodu w warsztatach szkolnych Defum uzyskiwali status pracownika młodocianego. Same warsztaty szkolne były wydziałem produkcyjnym fabryki , nazywanym w strukturach organizacyjnych jako P5. Produkowane przez uczniów proste części były wykorzystywane na zakładzie. Tym sposobem Defum co roku dostawał nowych pracowników . Znaczna część następnie kontynuowała naukę w technikum. W latach siedemdziesiątych dyrektorem szkoły był Stanisław Koziorowski ,a zastępcami J. Kalużny i A.Gębczyński. Wtedy na potrzeby szkoły, fabryki sponsorujące podjęły budowę internatu przy ul .Granicznej. Zmiany w Oświacie spowodowały ,że budynek ten nigdy nie został ukończony zgodnie ze swoim pierwotnym celem, natomiast na końcowym etapie przemianowano go w blok mieszkalny.
Autorzy tekstu: Tomasz Derda oraz Krzysztof Kulik
Źródła:
http://dabrowagornicza.naszemiasto.pl/artykul/przedstawiciele-ponar-defum-w-urzedzie-wojewodzkim,799204,art,t,id,tm.html
http://dabrowagornicza.naszemiasto.pl/artykul/dabrowski-defum-coraz-blizej-upadku,790586,art,t,id,tm.html
http://dabrowagornicza.naszemiasto.pl/artykul/ponar-defum-ma-juz-21-mln-zl-dlugu,803236,artgal,t,id,tm.html
http://dabrowagornicza.naszemiasto.pl/artykul/decyzja-w-rekach-komornika,393512,art,t,id,tm.html
http://dabrowagornicza.naszemiasto.pl/artykul/pracownicy-ponar-defum-pikieta-chca-ratowac-swoje-miejsca,360916,art,t,id,tm.html
http://dabrowagornicza.naszemiasto.pl/artykul/w-ponar-defum-czekaja-na-decyzje-wierzycieli,377834,art,t,id,tm.html
Początki historii
Historia Dąbrowskiej Fabryki zaczyna się w latach 70-tych XIX wieku. Na miejscu zakładu działa wtedy warsztat ślusarski bliżej nieznanego przemysłowca. Na jego bazie w 1882 roku R. Farkac założył fabrykę. Być może to on był właścicielem wspomnianego warsztatu. Zakład od samego początku do końca swoich dni działał na potrzeby przemysłu maszynowego. Na samym początku pracował dla przemysłu cukierniczego, lecz prawdopodobnie wytwarzał jedynie elementy maszyn, a nie składał całe urządzenia. Kolejnym krokiem w historii zakładu było wykupienie go przez A. Braunsteina. W krótkim czasie, bo już 3 lata od założenia fabryki w 1885 dołączył do niego znany czeski przemysłowiec Emil Skoda (ten sam który zapoczątkował produkcję czeskich aut,a nadto w Pilznie tj miejscu urodzenia Emila Skody do dzisiaj funkcjonuje fabryka obrabiarek
o nazwie SKODA Machine Tool a s , o asortymencie produkcyjnym bardzo podobnym do asortymentu DEFUM). W latach 90-tych zakład znów zmienił właściciela-tym razem stali się nim przemysłowcy z Sosnowca- Wilhelm Fitzner oraz Konrad Gamper. W 1897 roku przekształcili DEFUM w „Towarzystwo Akcyjne Zakładów Kotlarskich i Mechanicznych W. Fitzner i K. Gamper”. Była to jedna z najbardziej znaczących spółek w Królestwie Polskim, posiadająca swoje oddziały w Warszawie, Łodzi i innych ważnych miast carskich. Jestto swoisty kamień milowy w historii zakładu, który zaważył na jego dalszych losach. Zmiany w formie przedsiębiorstwa skonkretyzowały produkcję dąbrowskiej fabryki na przemysł maszynowy.
Filia giganta
Niestety dąbrowski zakład był jedynie filią o wiele większego zakładu w Sosnowcu-mieści się on obecnie niedaleko Centrum Handlowego Plejada. W Dąbrowie siła zainstalowanych maszyn parowych wynosiła jedynie 100KM, podczas gdy w Sosnowcu była to liczba dziewięciokrotnie wyższa. Ten okres historii stwarza dość spore problemy, gdyż często w źródłach ciężko jest rozdzielić czy informacje dotyczą konkretnie dąbrowskiego zakładu czy ogółu Towarzystwa Fitznera i Gampera. Filia nosiła wówczas nazwę "Dąbrowska Fabryka Maszyn i Odlewnia Żeliwa". Jedna z największych reorganizacji zakładu miała miejsce w okolicy 1910 roku – w zasadzie większość historycznych budynków została wybudowana w tamtym czasie, w tym istniejąca do dziś hala montażowa i hala odlewni. Poza różnego rodzaju frezarkami i tokarkami, które były wymienianie na bieżąco, to większość parku technologicznego i narzędziowego zakładu do samego wybuchu wojny pochodziła właśnie z tych lat.Produkcja skupiała się na urządzeniach mechanicznych, - tokarkach, frezarkach, szlifierkach, gwinciarkach, wiertarko-frezarkach, strugarkach i tym podobnych maszynach. Zakład świadczył również usługi w zakresie odlewów żeliwnych, mosiężnych i brązowych o wadze do 30 ton i ich późniejszej obróbce. Dynamiczny rozwój fabryki zahamował wybuch I wojny światowej. Podczas okupacji fabryka produkowała na rzecz niemieckiego przemysłu, ale spora część maszyn została zdewastowana lub wywieziona. Po konflikcie fabryka zmagała się z problemem braku zamówień.W tym celu W. Fitzner i K. Gamper założyli Fabrykę Lokomotyw w Chrzanowie - znany dziś jako Fablok. Dzięki fabryce w Chrzanowie dąbrowska fabryka miała zapewniony zbyt produkcji, a kolej z racji odbudowy państwa i braku odpowiedniego taboru w nowo utworzonym państwie stawiała szerokie perspektywy rozwoju. Ponadto z inicjatywy dyrektora Jechalskiego rozpoczęto równocześnie produkcję seryjną obrabiarek. Mimo ww. zabiegów firma nadal zmagała się z trudnościami. By się im przeciwstawić, o Od 1928 roku DEFUM wszedł do spółki „Zjednoczone Fabryki Maszyn Kotłów i Wagonów L. Zieleniewski, Fitzner i Gamper S.A”. Od tamtej pory usystematyzowano produkcję jedynie w kierunku kotłów oraz obrabiarek. Co ciekawe niemal połowa produkcji obrabiarek w 1933 roku była produkowana na potrzeby wojska! A dokładniej dla Marynarki Wojennej, Państwowej Wytwórni Uzbrojenia oraz Państwowych Zakładów Inżynieryjnych.
Produkcja odbywała się w następujący sposób. Po otrzymaniu zamówienia biuro fabrykacyjne przygotowywało specjalne karty - operacyjne, na których opisywano przebieg obróbki poszczególnych elementów zamówienia, oraz karty robocizny i materiałowe. kierowało go do modelarni.Tam wytwarzano modele odlewnicze z drewna ,które służyły do wykonywania form odlewniczych w których odlewano różnego rodzaju korpusy maszyn i innych urządźen. Oczywiście DEFUM posiadał magazyn odlewów, więc w przypadku identycznych zamówień korzystano z poprzednich modeli. Odlewnia wytwarzała 4 podstawowe rodzaje żeliwa oraz dwa specjalne o podwyższonych parametrach. Ciekawostka - zakład ściągał koks z Czech, z okolic Karwiny zamiast korzystać z polskiego. Niestety nasz, ze względu na dużą kruchość nie nadawał się do zastosowania w odlewni maszynowej. Następnym etapem po odlewni była czyszczarnia. Z niej półprodukty trafiały do warsztatu mechanicznego, gdzie po przywiezieniu dodatkowych elementów z magazynu głównego składano maszyny. Dalej wędrowały one do ekspedycji która wysyłała elementy do zamawiającego. W przypadku samych odlewów oczywiście omijano warsztat mechaniczny. Transport po terenie fabryki odbywał się po torach wąskotorowych, a do celów pociągowych używano wyłącznie koni. Zakład posiadał również bocznicę normalnotorową. Park maszynowy był bardzo różnorodny i rozbudowany. Najstarsze tokarki pochodziły w okresie międzywojennym pochodziły nawet z 1895 roku. Moc zainstalowana w zakładzie w 1933 roku wynosiła 140 KM w maszynach parowych i ponad 900 KM w silnikach elektrycznych.
W 1934 roku planowano w zakładzie otworzyć małe laboratorium na potrzeby odlewni metali. Z ciekawostek można podać iż np. w roku 1937 koszty produkcji wyniosły 1,8 mln ówczesnych złotych, w tym 1,1 mln przeznaczono na zakup materiałów, 330 tys. na pensje robotników, a 130 tys. na pensje urzędników. Dla porównania cena bochenka w tamtych latach to około 30 groszy. Krótko przed II wojną światową zakład przyjął nazwę Babock-Zieleniewski.
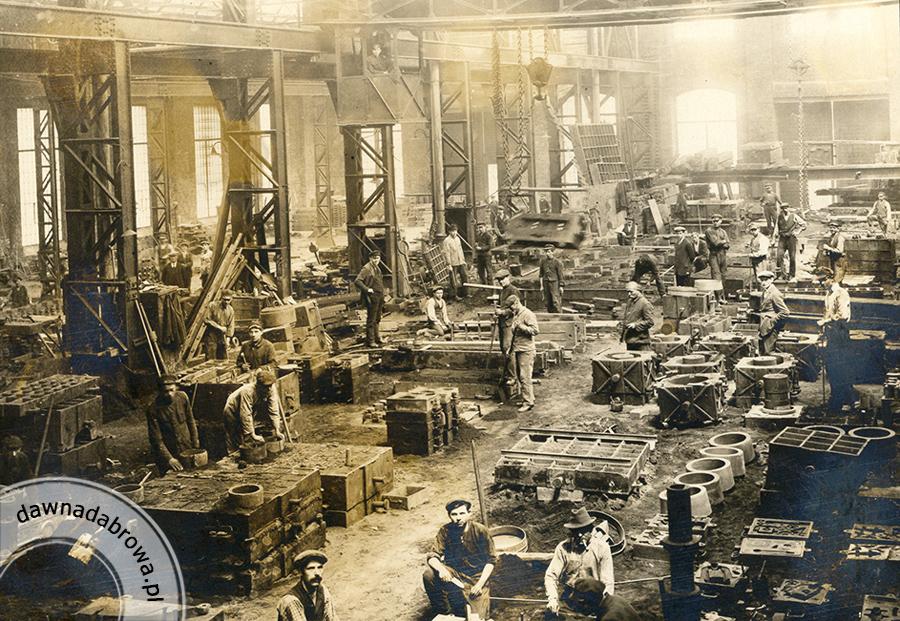
Fot. 1 Hala DEFUM w latach międzywojennych
II wojna światowa
Zakład przeszedł pod zarząd Trebsngeselsch Ost G.N.. W maju 1941 roku zakład został nabyty przez AG Ferrum. Zakład przez długi okres czasu produkował urządzenia na rzecz niemieckiej machiny wojennej. Produkcja została znacząco zitensyfikowana w stosunku do międzywojennej sytuacji - zatrudniano ponad 1000 pracowników i pracowano na trzy zmiany. Odlewnia została przeniesiona do Zabrza, a dotychczasowe pomieszczenia zajęła kolejna hala montażowa. Następne informacje są sprzeczne - jedne źródła podają że zakład został opuszczony przez okupanta zdewastowany, inne że wogóle nie zdążyli ruszyć ani jednej maszyny. W każdym razie Defum wrócił do pracy jeszcze w styczniu 1945 roku – przy czym trzeba wspomnieć iż Niemcy zostali wyparci z Dąbrowy dopiero 27 stycznia. Z polecenia Rady Zakładowej, kierownictwo powierzono inżynierowi Tadeuszowi Furdynowi. W marcu 1945 roku zakład przekazał Departamentowi Uzbrojenia 10 nowych obrabiarek. Ściągnięto również z powrotem odlewnię z Zabrza. Oprócz produkcji obrabiarek, zakład wykonywał również naprawy i remonty czołgów na potrzeby Ludowego Wojska Polskiego.
Złota era PRL-u
W czasach PRL DEFUM został upaństwowiony – dokładnie 30 listopada 1949 roku. Była to jedynie formalność, a zakład pracował dla państwa od samego końca wojny. Wraz ze zmianami własnościowymi przyszła zmiana nazwy na „Śląsko-Dąbrowska Fabryka Urządzeń Mechanicznych im. Stanisława Krzynówka”.2 lutego 1946 roku wyprodukowano setną obrabiarkę po II wojnie, a w listopadzie 1948 500-tnej. Oczywiście regularnie wykonywano plany wieloletnie, tak jak w każdym polskim zakładzie w tamtych latach. W 1950 roku wyprodukowano 35 tokarek-karuzelówek i 80 wiertarko-frezarek. W 1965 roku wyprodukowano 41 tokarek karuzelówek i 211 wiertarko-frezarek. Krótko po tym wydarzeniu rozszerzono asortyment produkcji o tokarki karuzelowe. W 1962 roku przyłączono do niego Szopienicką Fabrykę Obrabiarek.1964 rok przyniósł zmiany technologiczne. Przestarzałe modele obrabiarek CWC i HWC zostały zastąpione przez WFA-80 i WFA-100.
Kolejne zmiany organizacyjne przyszły w 1970. Na bazie czterech fabryk tj. FUM PORĘBA , DFO-DEFUM , Bielskiej Fabryki Obrabiarek oraz Jędrzejowskich Zakładów Mechanicznych został utworzony Kombinat Obrabiarek Ciężkich PONAR-PORUM . W 1975 nastąpiła nowa próba
integracji i tym razem utworzono Kombinat Obrabiarek Cięzkich PONAR-ZAWIERCIE który obejmował trzy fabryki tj. FUM-PORĘBA ,FO-RAFAMET i DFO-DEFUM . Żadna z tych koncepcji integracji nie zyskała jednak szerokiego poparcia poszczególnych zakładów i około roku 1980 powrócono do wcześniejszej samodzielności poszczególnych fabryk . Każda z fabryk
miała inną specjalizacje produkcyjną i każda z nich była uznanym producentem i eksporterem
swoich obrabiarek . Produkcja obrabiarek ciężkich w latach PRL-u była uznana za polską specjalność eksportową, a próby integracji tych znanych w świecie fabryk kończyły się rywalizacją o prym w połączonym kombinacie, co szczególnie było widoczne pomiędzy PORĘBĄ a RAFAMETEM.
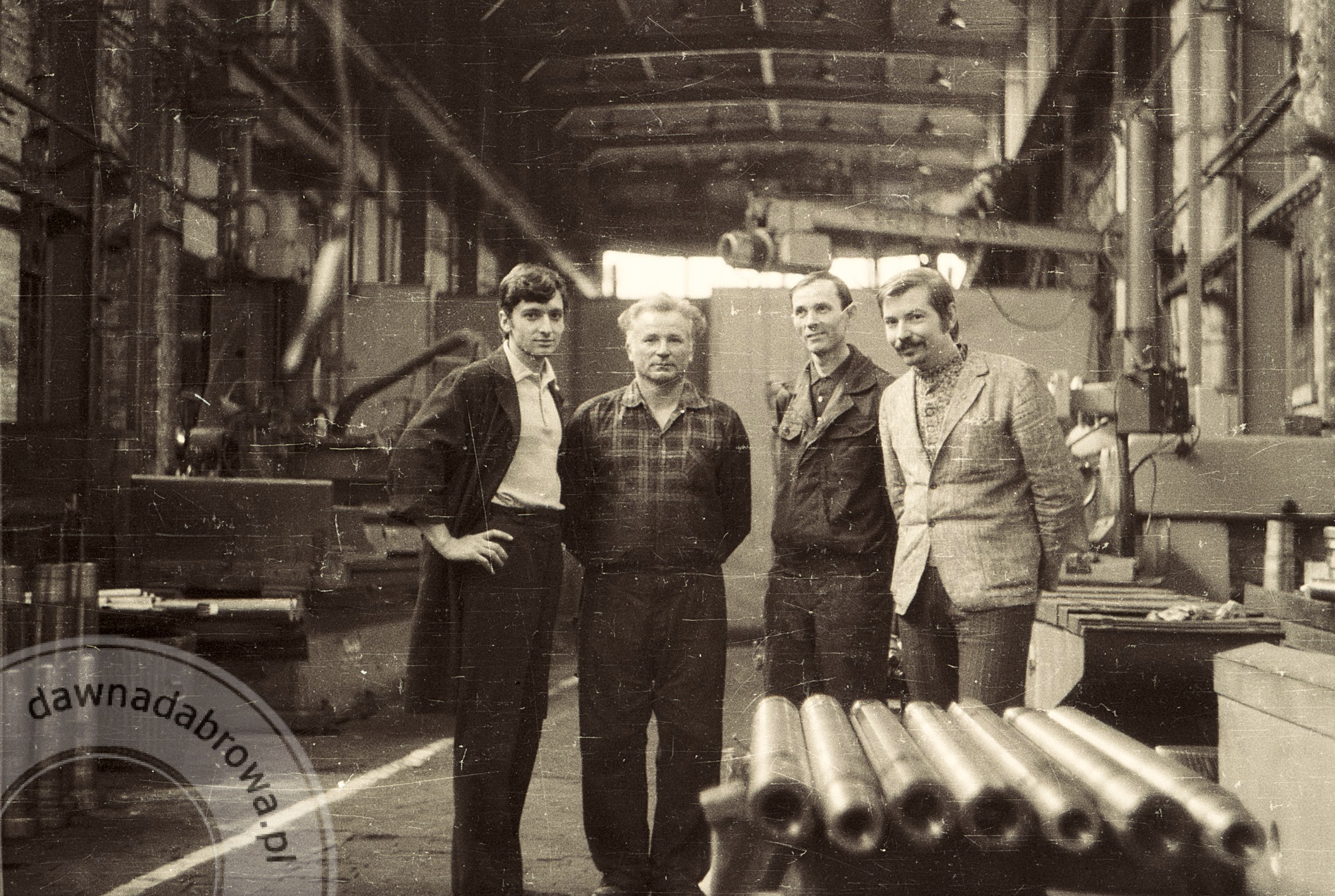
Fot.2 Zdjęcie hali produkcyjnej i pracowników, lata PRL-u
Obrabiarki, obrabiarki, obrabiarki...
Lata 70-te XX w to okres odbudowy przemysłu na całym świecie po zniszczeniach wojennych. Skutkuje to ogólnoświatową koniunkturą dla producentów dóbr inwestycyjnych dla przemysłu i w tym znacznym popytem na obrabiarki DEFUM.
Produkowane są wiertarko – frezarek i tokarki karuzelowe konwencjonalne a także początkowe serie obrabiarek sterowanych numerycznie z układami sterowania General Electric i Nucon -Asea. Okło 80 % produkcji jest eksportowane. W przedziale lat 1970 – 1975 eksport fabryki do krajów
zachodnich wzrósł o ok. 300 % Z fabryki wychodzą całe składy kolejowe wysyłane głównie do portu w Gdyni i dalej do krajów docelowych obu Ameryk a nawet Australii . Równolegle odbywa się dystrybucja drogą lądową do krajów Europy Zachodniej . Krajowi inwestorzy maja trudności w zakupie obrabiarek DEFUM gdyż eksport traktowany jest priorytetowo z uwagi na zarabianie niezbędnych dla kraju dewiz . W każdym miesiącu z fabryki wychodzi od 20-tu do 40-tu obrabiarek. W chwili uruchomienia produkcji każda obrabiarka ma już swojego docelowego odbiorcę .
Lata 70-te XX w obejmują produkcje n/w typów obrabiarek:
- Wiertarko -frezarki (licencja CERUTI) AD-100 ,AD-115,AD125
- Wiertarko-frezarka WFE- 100 i WFE100N
- Ciężkie wiertarko-frezarki płytowe WHB-150
- Centrum obróbkowe wiertarsko-frezerskie WFE 100 NM ,
- Centrum obróbkowe wiertarsko-frezerskie WFG-100 NM,
- Ciężka wiertarko-frezarka ADP-115,
- Tokarka karuzelowa KNA -110/135 A,
- Tokarka karuzelowa KNA -110/135 B,
- Tokarka karuzelowa KNA -110/135 N,
- Tokarka karuzelowa KNA -140/160,
- WFM-100 N i WFM-100 NM,
- Wiertarko-frezarka HWC-P 110A,
- Wiertarko-frezarka HWC-S 110A,
- Wiertarko-frezarka konwencjonalna ADS-115,
- Wiertarko-frezarka WFB-80,
- Wiertarko-frezarka WFB-80 S,
- Wiertarko-frezarka WFC - 90,
- Wiertarko-frezarka WFE - 100 A1 N,
- Wiertarko-frezarka WFG-100,
- Wiertarko-frezarka WFG-100 N,
- Wiertarko-frezarka WHB - 150,
- Wiertarko-frezarka WHC - 160,
- Wiertarko-frezarki poprzeczne WFE 100 A7 i WFE 100 A9,
- Wiertarko-frezarki WFE - 80 i WFE 100,
Wiertarko-frezarki WFM-100.

Lata 80-te i 90-te XX w to całkowite przejście do produkcji obrabiarek sterowanych numerycznie.
Powstają zupełnie nowe konstrukcje,stale doskonalone i modernizowane . Asortyment produkcyjny zostaje zawężony do wydajnych i konkurencyjnych obrabiarek wyposażanych w sterowania numeryczne SIEMENS, HEIDENHAIN i FANUC .
W tym okresie produkowane są:
- Wiertarko-frezarka sterowana numerycznie DBM 100 N , DBM 100NM , DBM 105N i DBM 105 NM
- Wiertarko-frezarka sterowana numerycznie WFS 130N i WFS 130NM
- Centrum obróbcze z magazynem narzędzi i systemem paletowym WFS130 NMP
- Frezarko-wytaczarka sterowana numerycznie FWA -1000CNC
- Frezarko -wytaczarka sterowana numerycznie WHA-130N
- Wiertarko-frezarka płytowa sterowana numerycznie WHD160N i WHD 180N
- Tokarka karuzelowa sterowana numerycznie KNA 110/135N
- Tokarka karuzelowa sterowana numerycznie KNA 140/160N
- Tokarka karuzelowa z kątowym pozycjonowaniem stołu KND 140/160N - -
- Wiertarko -frezarka z uchylnym wrzeciennikiem (6-osi CNC) WFZ60NW szczególności rodzina wiertarko -frezarek DBM ,tokarek karuzelowych KNA i wiertarko -frezarek płytowych WHD zyskały znaczący prestiż międzynarodowy i uznanie klientów w szczególności w USA, Niemczech, Turcji, a także na rynku krajowym. Warto wspomnieć tu
wybitnych konstruktorów – autorów tych autentycznie polskich wyrobów. Niekwestionowanym liderem był inż. Tadeusz Białas (1951-2017)- innowator techniczny, twórca wielu nowych rozwiązań , znany pasjonata obrabiarek i uznany w Polsce i na świecie praktyk i osoba potrafiąca rozwiązać każdy temat. Z nim współpracowali mgr inż. Zbigniew Robak ,inż Zbigniew Bałdys, inż Jerzy Supernak, mgr inż. Stanisław Kaczorowski, mgr inż. Włodzimierz Rudy oraz Ryszard Lasota.Defum był zakładem chronionym, ze względu na fakt iż duża część obrabiarek była produkowana dla wojska. Powstawały tu specjalne maszyny które odpowiadały za produkcję i regenerację luf do czołgów, dział i innego rodzaju sprzętu wojskowego. Wyroby dąbrowskiej fabryki trafiały do odbiorców na całym świecie – USA, Anglii, Niemcy, Japonii, Holandii, Norwegii, Iranu, Jemenu, Jordanii, Brazylii, Turcji. Warto również wspomnieć iż dąbrowskie obrabiarki były częstymi gośćmi na wszelakiego rodzaju targach przemysłowych. W archiwach strony znajduje się szereg zdjęć z tego rodzaju wydarzeń. W 1978 r. maszyny DEFUM prezentowane były – oprócz Międzynarodowych Targów Poznańskich – na dwunastu międzynarodowych imprezach wystawienniczo-handlowych, min. w Paryżu Coventry (W. Brytania), Atenach, Buenos Aires i Helsinkach.Po 2000 roku następuje gwałtowne załamanie koniunktury na obrabiarki. Centrala Handlu zagranicznego- Metalexport odstępuje od wykupu wcześniej zakontraktowanch maszyn przeznaczonych na rynki eksportowe .Fabryka pozostaje z wyprodukowana masą towarową i znacznie zaawansowaną produkcją w toku , bez możliwości szybkiej sprzedaży . Taki stan zakłócapłynność finansową przedsiębiorstwa. Mimo to, w tej wyjątkowo trudnej sytuacji DEFUM pozyskuje bardzo prestiżowe ,ale również obarczone znacznym ryzykiem kalkulacyjnym i terminowym kontrakty. Za absolutnie fenomenalny uznać należy fakt ze właśnie w tym okresie (w
szczególności w przedziale lat 2002 do 2006 powstają innowacyjne i jednostkowe rozwiązania techniczne . Główne z nich to: - Wiertarko-frezarka do obróbki wielkogabarytowych kół zębatych i bieżni łożyskowych dla potrzeb górnictwa odkrywkowego węgla brunatnego dla KWK-Bełchatów
- Szlifierka TACC 413 projektu dr. inż Stanisława Zewelda do obróbki komory nabojowej armaty okrętowej dla przemysłu obronnego na zlecenie Ministerstwa Obrony Stanów zjednoczonych.
- Podwójne centrum obróbcze DUBLER+WHC 160NMS do obróbki korpusów czołgów dla krajowego przemysłu obronnego.
- Wiertarko -frezarka do obróbki bloków węglowych dla potrzeb hutnictwa stali w Polsce i na świecie
- Zespół obrabiarek do obróbki kokili do produkcji felg aluminiowych dla firmy Stalschmidt Maiworn w Stalowej Woli
- Modernizacja obróbki walców pielgrzymowych w przemyśle hutniczym w kraju i Republice Czeskiej
- Szlifierka do interpolacyjnego szlifowania korpusów pomp dla kontrahenta niemieckiego.Każde z w/w pozycji to nowe rozwiązania techniczne. Fabryka zyskuje uprawnienia do prowadzenia prac badawczo-rozwojowych .Te rozwiązania i ich przydatność dla przemysłu i gospodarki są dostrzeżone przez Naczelną Organizacje Techniczną która wspiera starania Defum w pozyskaniu
funduszy pomocowych na restrukturyzacje przedsiębiorstwa. Zachodząca w tym czasie transformacja gospodarcza ukierunkowana jest jednak na prywatyzację gospodarki a skrajnie na likwidacje podmiotów wykazujących problemy finansowe. Proces naprawczy i restrukturyzacja fabryki najbardziej i skutecznie udaje się w rozwoju umiejętności reakcji na potrzeby rynku przemysłowego i indywidualne podejście do potrzeb klienta. Nie jest możliwe jednak długotrwałe kontynuowanie działanń innowacyjnych i badawczo-rozwojowych bez wsparcia kapitałowego.i
niezbędnych inwestycji . Defum nigdy nie otrzymuje żadnych środków pomocowych na ten cel. Pomimo wielu innych pozytywnych działań i starań od 2006 roku zaczyna się stagnacja fabryki i powolne zamykanie działalności .W 2010 roku zorganizowano strajk i pikietę pod urzędem miejskim. Zakład posiadał wtedy 12 milionów długów, jego przejęciem był zainteresowany Rafamet SA z Kuźni Raciborskiej. Zamknięcie i zwolnienie pracowników nie obyło się bez pikiety i wizytacji w urzędzie miejskim. Ostatecznie od 2015 roku DEFUM zostaje zamknięte. Był to ostatni zakład państwowy w województwie śląskim.
Zakład posiadał dwa loga – stworzone w PRL składało się z niebieskiego koła, którego obwódkę górnej części stanowiło koło zębate, a dolnej wieniec laurowy. W koło była wpisana kursywą i podkreślona nazwa zakładu – „Defum”. Drugim logiem zakładu były trzy litery „DFO” zamknięte w kole zębatym.
Pomieszczenia fabryczne
Defum to ogromny zakład składający się z tysięcy pomieszczeń, hal, magazynów, poddaszy. Opisanie każdego najdrobniejszego szczegółu zajmie bardzo dużo czasu i będzie stopniowo rosło z czasem. W celu dokładniejszego poznania zakładu ponumerowałem wszystkie budynki na mapce.
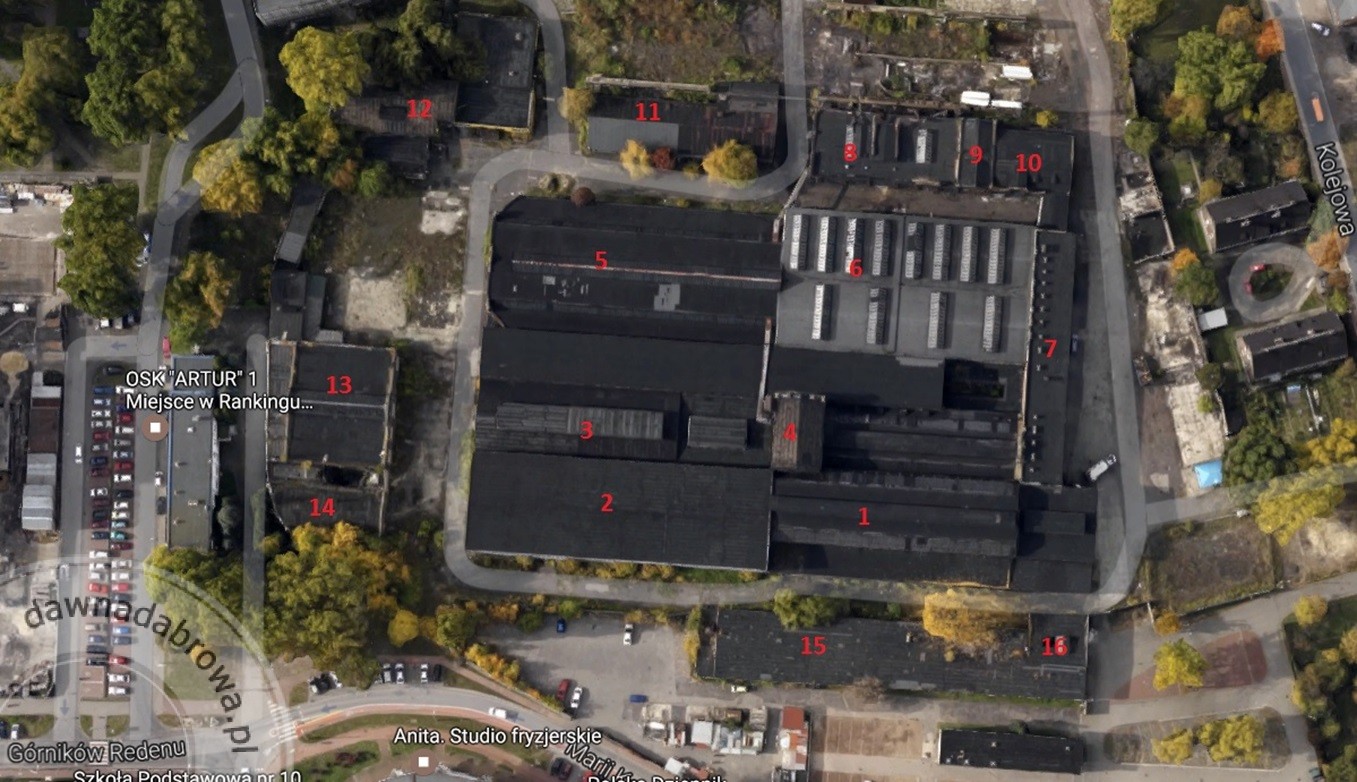
Główny człon zakładu stanowi zespół hal fabrycznych ponumerowanych od 1 do 6. W okresie międzywojennym wyróżniały się na tle pozostałych zakładów w okolicy. Były bardzo przestronne, doskonale oświetlone, wentylowane i zelektryfikowane. Zostały utrzymane w secesyjnym stylu
Hala numer 1
Hala ta pochodzi z okresu międzywojennego. Zastąpiła wcześniejszą halę z XIX wieku. Wykonana została w technice stalowo-ceglanej w kształcie odwróconej litery „T” w stylu modernizmu. Główny środkowy trzon stanowił trapezoidalny, oszklony dach, a po obu bokach symetrycznie ciągnęły się niższe partie hali. Pomiędzy cegły umieszczono żelazne pręty wzmacniające konstrukcję. Jej wschodnia oraz północna ściana zostały zachowane względnie oryginalnym stanie. Sama konstrukcja nie została zmieniona, wymieniono jedynie szkło na materiał z tworzywa sztucznego i dodano PRL-owskie instalacje techniczne. Północna fasada hali była pozbawiona ozdób architektonicznych – jedynym ciekawym elementem było ogromne przeszklone okno. Z tej strony do zakładu dochodziła bocznica kolejowa, która przez bramę mogła wjechać do wewnątrz hali. Wschodnia część hali składa się z ciągnących przez całą długość okien oraz ozdobnego grzymsu pod linią dachu. Niegdyś hala była o wiele dłuższa i kończyła się mniej więcej w miejscu dzisiejszej hali nr 2, jednak w PRL ściany tej części zostały wyburzone. Możemy się jednak domyślać iż była utrzymana w identycznym stylu architektonicznym. Od zachodniej strony przylega W środku hala nr 1 prezentuje się naprawdę okazale. Co kilka metrów stoją ogromne, kilkumetrowe secesyjne żelazne słupy podtrzymujące konstrukcję dachu. Warto zwrócić uwagę na ich nitowanie. Górny, trapezoidalny dach był utrzymany przez przepiękny, stalowy szkielet na którym były umieszczone przemysłowe lampy. Konstrukcja dachu była drewniana. Większość przestrzeni nie była podzielona żadnymi ściankami działowymi i stanowiła jeden kompleks. Jedynie po wschodniej stronie znajdowało się jedno piętrowe pomieszczenie socjalne (dziś już praktycznie wyburzone) oraz zabudowana transformatorownia – obecnie wybebeszona, prawdopodobnie zostanie wyburzona.. Co ciekawe na dachu tej hali znajduje się WPO- Wieżowy Punkt Obserwacyjny, system obrony przeciwlotniczej z okresy lat 50-tych.
W hali znajdowała się odlewnia żeliwa, która wykonywała odlewy na potrzeby produkowanych w DEFUM maszyn. Do przygotowanych w innych budynkach modeli wlewano ciekły metal. W PRL była podzielona na dwie części. Jedną z nich była karniarnia - to część wydziału gdzie wykonywało się rdzenie formierskie. Kranistą nazywano - suwnicowego, który „jeździł kranem” co dziś może brzmieć trochę zabawnie. Jak łatwo się domyślić była to osoba odpowiedzialna za wlewanie materiału do form.
Kastlami nazywano skrzynie formierskie, a giserami formierzy. W 1974 roku zlikwidowano starą odlewnię, a halę zaadaptowano na dział obróbki mechanicznej i cieplnej.
Hala nr 2
Historia hali jest bezpośrednio połączona z halą nr 1, gdyż do PRL-owskiej przebudowy stanowiły jedną integralną część. W późniejszych latach wyburzono boczne ściany, zachowując jedynie samą konstrukcję oraz dach. Ściany zostały podwyższone do jednolicie wysokiego prostokątnego kształtu i obłożone blachą falistą. Również w ten sam sposób zabudowano okna dachowe, pzostawiając jedynie dwa wąskie pasy okien na bocznej ścianie.
Hala nr 3
Jest to kolejna historyczna hala która prawdopodobnie powstała wraz z pozostałymi zabudowaniami. Przyklejona jest do zachodniej ściany hali nr 1 Niegdyś stała wraz z nią osobno i nie była przyklejona do innych zabudowań. Jednak w wyniku przebudowy fabryki zachodnia i południowa ściana stały się niejako ściankami działowymi większego kompleksu. Nie zostały na szczęście wyburzone, poza wyjątkiem w miejscu bramy między halami, a jedynie zamurowane.
Za ściany zaadaptowano zewnętrzne fasady historycznych hal. Nie zostały one wyburzone, a jedynie za- i nad-budowane. Dzięki temu w przyszłości będziemy mogli wrócić do pierwotnego stanu. W środku znajdowała się wydzielona siatką przestrzeń oraz umieszczone na wysokości pierwszego piętra warsztaty. Powyżej opisane pomieszczenia dodatkowe są z duża dozą pewności wytworem PRL-u – w oryginalnym projekcie hala nie była przedzielona żadnymi dodatkowymi pomieszczeniami. Wyjątek stanowi wiszący nad halą magazyn w południowo-zachodnim rogu hali nr 1. Jest to pomieszczenie znajdujące się pod wieżą wodną zakładu opisanej w punkcie 4.
Wieża wodna 4
Wieża wodna istnieje od samego początku zakładu. Jest niejako wklejona w halę fabryczną. Na poziomie gruntu w niczym pod wieżą znajduje się po prostu pusta przestrzeń hali. W zachodnim rogu znajduje się metalowa klatka schodowa prowadząca na wyższe kondygnacje. Na wysokości pierwszego piętra znajduje się „wiszące” pomieszczenie magazynowe. Z niego wchodzimy schodami do górnej części – właściwej wieży wodnej. Dziś jest to puste pomieszczenie, lecz kiedyś mieściło ono nitowany, metalowy zbiornik wody używanej do procesów technologicznych. Wraz z przyłączeniem DEFUM do sieci wodociągowej przestała mieć znaczenie i prawdopodobnie została zmieniona w magazyn.
Hala nr 5
Ten budynek był głównym sercem zakładu. To tutaj znajdowała się montownia maszyn mechanicznych. Jednocześnie był to najbardziej bogaty w detale budynek fabryki. Głównym elementem architektonicznych bocznych fasad były ceglane pilastry dzielące go na segmentu. Pomiędzy nimi znajdowały się półkoliste, przestronne okna. Każde z nich posiadało bogaty zdobione nadproże, i szereg grzymsów. Frontowa fasada hali, od strony południowej składała się z osi czterech kolumn – dwóch bocznych i dwóch środkowych. Ich szczyty zostały zwieńczone okręgami i frezami. Między środkowymi kolumnami umiejscowiono trójkątny szczyt u góry, a pod spodem przestronne okno z ozdobnym nadprożem ze zwornikiem. Po obu stronach symetrycznie znajdowały się bramy do zakładu, dziś zamurowane. Możliwe że w czasach przedwojennych w półkolu umieszczonym na środku fasady znajdowało się logo zakładu. W środku hali znajdziemy również wspaniałe, secesyjne żelazne słupy oraz stalowy szkielet konstrukcyjny drewnianego dachu. Jej zachodnia strona została w PRL-u zabudowana piętrowymi warsztatami, ale pozostała część gmachu stanowi jedną całość nie przedzieloną żadnymi ściankami działowymi.
Hala nr 6
Budynek początkowo stanowił jedność z halą nr 5. Przebudowie uległy ściany zewnętrzne które zostały znacząco podwyższone, oraz dach. Część żelaznych słupów wewnątrz pochodzi z pierwotnej, XIX wiecznej hali. Nie wiem niestety czy przebudowa została wykonana jeszcze przed wojną czy już w czasach PRL-u.
Biurowiec nr 7
Budynek powstał we wczesnych latach PRL-u, zastąpił pierwotny budynek dyrekcyjny mieszczący się po prawej stronie bramy wjazdowej, dziś już wyburzony. Biurowiec posiada połączenie z halami produkcyjnymi na parterze(przez portiernię) oraz na piętrze(przez szatnię). W środku znajdziemy symetryczny układ jednakowych biur po obu stronach korytarza i zwyczajną klatkę schodową. Warto jednak zwrócić uwagę na interesujące, prostokątne balustrady. Wewnątrz biurowca znajdowały się biura zarządu, punkt wymiany i reperacji odzieży, dział produkcji, kasa, portiernia, archiwum, powielarnia dokumentacji, dział kadr i organizacji pracy, centrala telefoniczna, dział marketingu i handlu, dział techniczny TKT, sekretariat, biuro dyrektora naczelnego i jego zastępcy, dyrektora produkcyjnego i jego zastępcy.
Kotłownia nr 8
Budynek powstał w 1910 roku. Składa się z dwóch symetrycznych i identycznych członów. Pierwotnie, przed wojną tylko część południowa stanowiła kotłownię, a druga halę maszyn. W PRL połączono je w jedną funkcję kotłowni. Fasadę stanowią cztery kolumny, między którymi umieszczono trzy przestronne okna z nadprożami połączonymi zwornikiem. W środkowej części tuż pod linią dachu w okręgu umieszczono datę budowy. W środku znajdują się dwa kotły ciepłownicze i szereg pomieszczeń technicznych. Dach prawdopodobnie został przebudowany w PRL-u.
Budynki techniczne nr 9,10,11, 12
Wszystkie budynki pochodzą sprzed II wojny światowej. Ich fasady wykonano w podobnym stylu do reszty budynków. Zobaczymy tu ozdobione ceglanymi nadprożami okna oraz gzymsy między kondygnacjami. Przed wojną budynek nr 9 pełnił funkcję łaźni, numer 10 wozowni, stajni oraz kasyna. W PRL mieścił się tam skład obrony cywilnej, warsztat napraw(parter) i magazyn części elektrycznych(na piętrze). Budynek nr 11 to magazyn fabryczny. W PRL zorganizowano w środku dział obróbki cieplnej, do dziś można zobaczyć pozostałości pieców oraz kadzi. Budynek nr 12 to skład modeli na potrzeby odlewni, funkcję te zachował od czasów międzywojennych do końca PRL-u. W środku znajduje się niewielka suwnica, klatka schodowa i pomieszczenia magazynowe. Wokół niego znajdowały się budynki wybudowane w PRL-u – m.in. skład chemikaliów.
Budynki techniczne nr 13,14,15,16
Budynek nr 13 to czyszczarnia wybudowana w 1912 roku. W środku czyszczono wykonane w odlewni części do maszyn. Budynek numer 14 przed wojną mieścił składnicę odlewni, w PRL zmieniono jego funkcję ( niestety nie znaną mi). W okresie przedwojennym w budynku nr 15 znajdował się magazyn główny, ekspedycja oraz sprężarnia. W latach 60-tych budynek został znacząco przebudowany, możliwe że został wyburzony do fundamentów. Na jego miejsce powstała narzędziownia. Parter zajmowała długa hala posiadająca niegdyś niewielką suwnicę. Na piętrze znajdowały się biura-tak jak wskazują tabliczki na drzwiach sekcja technologiczna, zakupu narzędzi, wynalazczości. Budynek nr 16 to przedwojenna kuźnia, praktycznie w stanie ruiny. Warto w tym miejscu wspomnieć jeszcze o znajdującej się między halami niewielkiej remizie strażackiej.
W latach PRL-u w DEFUM działały cztery oddziały: obróbki mechanicznej, mechanicznej ciężkiej, mechanicznej lekkiej oraz montażu. W 1966 roku na zakładzie wybudowano nową hale montażową wraz z zapleczem socjalnym. W latach 1969-71 wybudowano nowoczesny biurowiec który pomieścił biuro konstrukcyjne. W tym samym czasie przeprowadzono remont głównej hali montażowej. Co najmniej od 1972 do 1976 roku zakład posiadał własną, 3-letnią szkołę zawodową, która mieściła się w budynkach dzisiejszego ZST oraz orkiestrę dętą. Pojawiają się również relacje o szkole zawodowej działającej w latach 1945-1950 w prywatnym budynku na ulicy Bolesława Limanowskiego.
Kadry i społeczność
Bardzo ważnym elementem zakładu były kadry i ich doskonała współpraca. Dzięki niej i odpowiedniemu podejściu kierownictwa do zwykłych pracowników zakład odnosił sukcesy. W roku 1913 fabryka zatrudniała 376 robotników i 55 urzędników. Nie zatrudniano wtedy kobiet, choć w latach 1900-1913 aż 5% załogi stanowili młodociani przed 18 rokiem życia.
Wraz z nadejściem ery PRL-u w fabryce rozwinęło się zaplecze socjalne. Pojawiły się domy fabryczne, wczasy pracownicze, ambulatorium, świetlica zakładowa. Wprowadzono bezpłatną odzież roboczą, zaczęto szkolenia pracowników w technikum w Bytomiu. W późniejszym okresie zakład otworzył własną szkołę na ulicy Bolesława Limanowskiego, opisaną w oddzielnym rozdziale. W fabryce utworzyły się koła Towarzystwa Przyjaźni Polsko-Radzieckiej, Liga Kobiet, Koło Wynalazców.
Kolejni dyrektorzy:
- Gustaw Mazurkiewicz
- Michał Świerzyński
- Smolarski
- Konrad Gamper
- Giestych
- Zybert
- 1916-1933 Edward Stypułkowski
- 1933-1939 Mieczysław Zieleniewski
- Kindler
- Hedwig
- Artur Kropt
- 1.02.1945 -20.02.1947 Tadeusz Furdyn
- 20.02.1947 -6.06.1948 Zygmunt Nawrocki
- 6.05.1948 -1.01.1950 Tadeusz Domański
- 1.01.1950-07.05.1954 Stanisław Szczygieł
- 07.05.1954 - 12.8.1955 Stanisław Kotuła
- Od 12.8.1955 Marian Kuchta
- Bogdan Dziubiński
- Tomasz Derda
W okresie ok. 1890-1914 struktura zarządu przestawiała się następująco:
- Dyrektor: Konrad Gamper.
- Dział Techniczny: J. Musil.
- Księgowość i rachunkowość: M. Bernard.
- Administracja: St. Gertych
- Dział zakupów: G. Modlinski
- Dział sprzedaży: F. Nebroj.Z dawnych gazet wiemy że redukcje pracowników w latach 30-tych nie ominęły również tego zakładu.
- Struktury w 1933 roku przedstawiają się następująco:
- Dyrekcja: Inż. Mieczysław Zieleniewski,
- Biuro Fabrykacyjne: wakat, zastępstwo Dąbrowski,
- Główny Konstruktor: Artur Kropf ,
- Biuro Techniczne: wakat, zastępstwo Inż. Mieczysław Zieleniewski,
- Biuro Administracyjne: Aleksander Nobis,
- Biuro Zakupów: wakat, zastępstwo Aleksander Nobis,
- Kierownik Warsztatu: Ferdynand Nebroj,
- Kierownik Odlewni: Gabryel KniagininW 1928 roku w fabryce było zatrudnionych 402 robotników, a z powod kryzysu w miesiącach letnich 1932 roku w fabryce było jedynie 60 pracowników.Struktury w 1937 roku przedstawiają się następująco:
- Kierownik Wytwórni: Inż. Mieczysław Zieleniewski,
- Biuro Fabrykacyjne: Tadeusz Furdyn,
- Biuro Konstrukcyjne: Artur Kropf ,
- Biuro Ofertowe: Ferdynand Nebroj
- Biuro Administracyjne: Aleksander Nobis
- Biuro Zakupów: Karol Matkowski
W tym miejscu chciałbym rozwinąć strukturę Biura Fabrykacyjnego, które dzieliło się na: - Oddział Odlewni
-Modelarnia
-Odlewnia brązu
-Odlewnia Żeliwa
-Czyszczarnia - Magazyn Główny
- Oddział Warsztat Mechaniczny
-Obróbka części
-Rewizja
-Montownia
-Kuźnia
-Narzędziownia - Magazyn Fabrykacji
- EkspedycjaNależy tu wspomnieć że Artur Kopf , główny kosntruktor był jedynym obcokrajowcem w fabryce - Czechosłowakiem pochodzenia niemieckiego.1933 rok to średnie zatrudnienie około 145 robotników, w tym około 15% młodocianych. W całym zakładzie była wówczas zatrudniona jedna kobieta. W 1937 roku w zakładzie było zatrudnionych 390 pracowników, w tym 31 umysłowych( w tym 5 kobiet), 359 fizycznych(w tym tylko jedna kobieta).Rok 1939 to już 600 pracowników. W listopadzie 1945 roku w Fabryce pracowało 650 robotników, w tym 100 kobiet.DYREKTORZY DEFUM OD 1945 ROKU
- Tadeusz Ferdyn – dyrektor naczelny od 1945r
- Marian Kuchta - dyrektor naczelny od brak danych
- Stanisław Krupa – dyrektor naczelny od 1964,
- Włodzimierz Szczerba – z-a dyr. ds technicznych
- Tadeusz Płocki -z-ca dyr. ds produkcji
- Bogdan Dziubiński -dyrektor naczelny od 1974
- Ferdynand Flak – z-ca dyr.ds technicznych
- Adolf Szarama – z-ca dyr. ds produkcji
- Andrzej Kuczabiński – dyrektor naczelny od 1989
- Leszek Stasiński -z-ca dyr ds technicznych
- Marian Witas -z-ca dyr ds produkcji
- Wiesław Gęborski -z-ca dyr. ds tech.-prod.
- Wiesław Gęborski - dyrektor naczelny od 1990
- Kazimierz Podsiadło- z-ca dyr ds handlowych
- Tomasz Derda – z-ca dyr ds tech.-prod. od 1990
- Tomasz Derda – dyrektor tech. -prod.od 2000 do 2007
ZNACZĄCE OSOBY KADRY TECHNICZNEJ I KIEROWNICZEJ PO 1945 ROKU
- Przewodniczący Rady Zakładowej Jan Biskup,
- Główny Konstruktor i specjalista od obrabiarek sterowanych numerycznie dr. inż. Leszek Stasiński oraz mgr inż Bonifacy Kopeć (lata sześćdziesiąte i siedemdziesiąte XX w),
- Główny Specjalista d/s Organizacji inż Władysław Włoch,
- Główny Specjalista d/s Osobowych Stanisław Roziach,
- Główny Specjalista d/s Eksportu Bonifacy Kopeć,
- Zastępca Dyrektora d/s Produkcji , Główny specjalista ds eksportu i zbytu Adolf Szarama,
- Zastępca Dyrektora d/s Ekonomicznych mgr Grażyna Mazur,
- Zastępca Dyrektora d/s Technicznych ,kierownik działu eksportu i zbytu mgr. inż. Włodzimierz Szczerba, później Ferdynand Flak,
- Szef Produkcji inż. Tadeusz Płocki,szef oddziału zamiejscowego w Katowicach Szopienicach
- I sekretarz Komitetu Zakładowego POP PZPR inż. Ryszard Kryjak ,a później inż. Henryk Bargieł,
- Przewodniczący Komitetu Samorządu Robotniczego - Janusz Hejdys,
- Kierownik Działu Spraw Osobowych Romuald Kaczmarek,
- Główny Technolog i racjonalizator okresu powojennego Kazimierz Kopydłowski
- Kierownik Zakladowego Ośrodka Techniki OSN,Szef Produkcji mgr inż. Władyslaw Lach.
- Główny Technolog, dyrektor produkcji inż. Marian Witas
- Zastępca głównego konstruktora ds elektrycznych, kierownik Wydziału Montażu inż Janusz Kaczmarzyk ,
- Główny Elektronik mgr inż. Jerzy Krzemień
- Główny Technolog mgr. Włodzimierz Pałasz
- Zastępca dyr. d/s ekonomicznych-inż. Bohdan Skiba
- Główny Elektronik ,później kierownik serwisu , udziałowiec Mexpol Niemcy mgr inż. Adam Barański
- Główny konstruktor, wybitny specjalista konstruktor, pasjonata obrabiarek, ceniony wśród kontrahentów fabryki w kraju i na świecie inż. Tadeusz Białas
- Główny specjalista ds eksportu i zbytu inż. Zbigniew Tafil
- Kierownik Wydziału Montażu,Szef Produkcji, Główny specjalista ds Eksportu i Zbytu z-ca dyr ds prod. dyrektor mgr inż. Wieslaw Gęborski
- Kierownik Wydz. Obróbki Mechanicznej Zygfryd Wężowicz
- Kierownik Oddziału w Katowicach-Szopienicach Józef Zralek
- Główny specjalista ds eksportu i zbytu, dyrektor handlowy mgr inż. Kazimierz Podsiadło
- Dyrektor techniczny ,później dyr naczelny FUM Poręba mgr inż. Ferdynand Flak .
- Główny mechanik, Główny Technolog, kierownik obr. mechanicznej inż. Janusz Cupiał
- Kierownik kooperacji, kierownik zaopatrzenia, kierownik obróbki mechanicznej Janusz Kmita
- Kierownik wydz obróbki mechanicznej Janusz Jagus
- Kierownik Oddz. W Katowicach -Szopiennicach,później prezes Profum Sp.zoo. Kazimierz Złoty
- Kierownik wydz Montażu, główny specjalista ds inwestycji i rozwoju, Szef produkcji dyrektor techniczno-produkcyjny, później Prezes Zarządu ZMUW Sp.z Sosnowcu mgr inż. Tomasz Derda
- Ryszard Kryjak- inż. kierownik Wydz. Montażu
- Kierownik Montażu Tadeusz Szwarcer
- Główny specjalista ds. kontroli jakości mgr inż. Stefan Jędras
- Główny technolog i główny specjalista ds. zbytu i eksportu mgr inż Bernard Jaskuła ,
- Główny technolog - mgr inż. Lubomira Bagińska
- Kierownik Działu Zaopatrzenia mgr Grzegorz Dolniak (później poseł na sejm RP, zginął w katastrofie smoleńskiej)
- Kierownik działu Przygotowania produkcji ,kierownik działu zaopatrzenia Marian Rak
- Kierownik Wydziału Obróbki Mechanicznej- Janusz Hejdys
- Kierownik Dz. BHP - Jan Siedlecki
- Kierownik Ośrodka Maszyn Analitycznych- mgr Zbigniew Czekaj
- Główny Mechanik- inż. Zenon Pawelec
- Główny Energetyk-mgr inż.Zdzisław Flak
- Główny spec. d/s ekonomicznych-mgr Magdalena Wawrzynczak
- Główny Energetyk - inż Bogdan Doktór
- Główny Księgowy- Emilia Jagiełko
- Główny Księgowy mgr Krystyna Lupa
WSPÓŁPRACA NAUKOWO-TECHNICZNA - Prof. dr hab. Jerzy Jędrzejewski- Politechnika Wrocławska
- Prof. dr hab. Jan Kosmol- Politechnika Ślaska
- Dr inż. Ewald Olszewski- Politechnika Częstochowska
- Dr inż. Stanisław Zeweld- TZE-Tacone Zeweld Engineering z siedzibą w Opolu (Biuro inżynierskie działające na zlecenie kontrahentów z USA)
- Dr inż. Wojciech Ratyński -Naczelna Organizacja Techniczna z siedzibą w Warszawie
- Spółka Inżynierska Polteron-Inwest z siedzibą w Krakowie
- Instytut Obróbki Skrawaniem w Krakowie
- Centralne Biuro Konstrukcji Obrabiarek w Pruszkowie
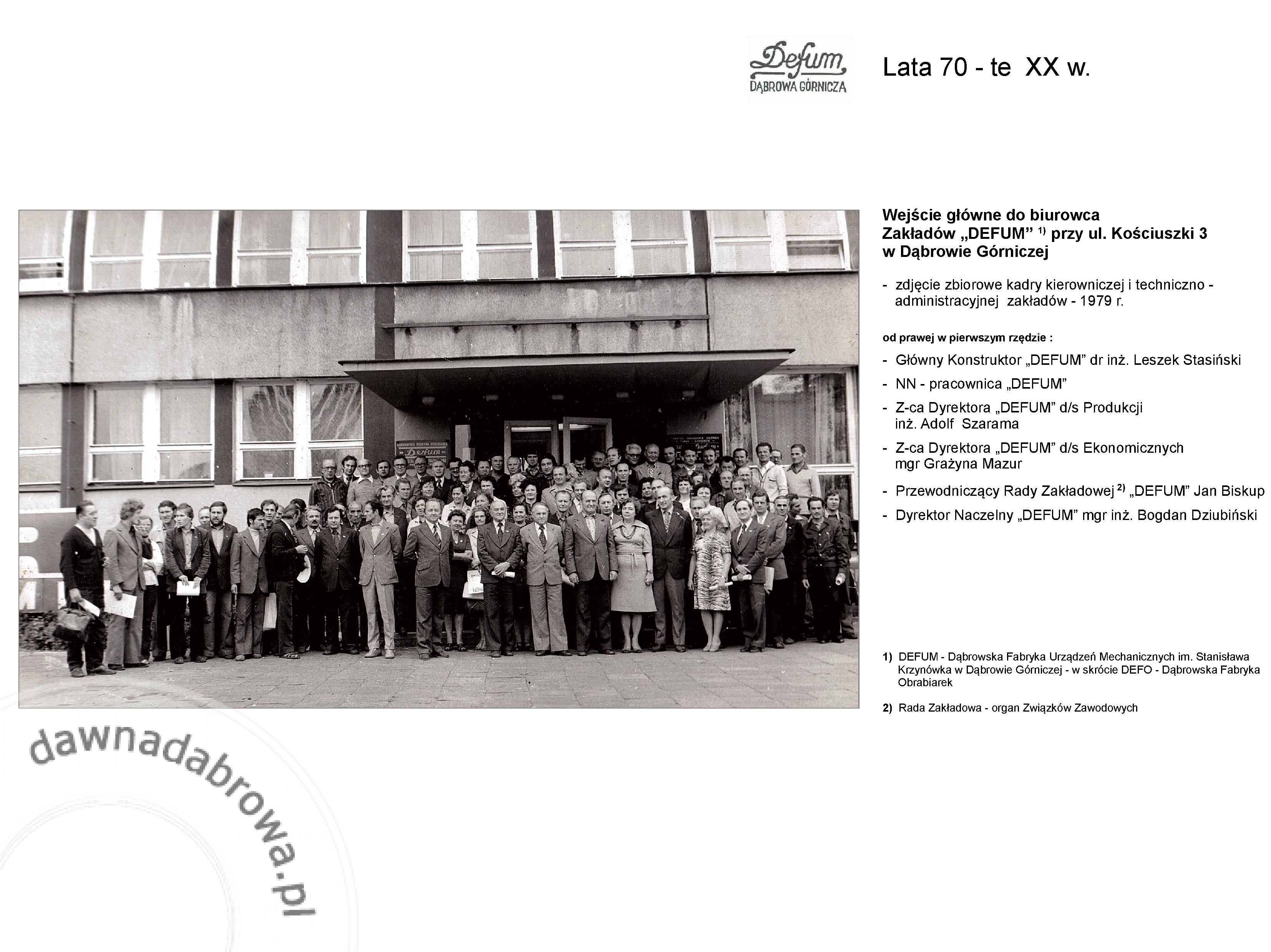
Pracownicy Defum obchodzili Dzień Metalowca. Wydarzenie uświetniała gala na deskach Pałacu Kultury Zagłębia.
W 2003 roku pracowało 300 osób, w 2010 110 pracowników a w 2011 80.
Zarządcy komisaryczni i likwidatorzy w okresie 2000 do 2015 roku:
Wojciech Miszczyk ,Mirosław Urbańczyk, Roman Sowiński , Wiesław Kaczmarski, Małgorzata Haładyj ,Anna Michałek ,Barbara Szkoda ,Jacek Wanic, Krzysztof Wrona (likwidator od 2013)
Statystyki Produkcji:
1933 rok - 20 obrabiarek, 600 ton odlewów i armatury
1937 rok - 77 obrabiarek, 1210 ton odlewów i armatury, zużywając 2000 ton surowców metalowych i 1200 ton paliwa w postaci węgla i drewna
1977 r. -165 obrabiarek, z czego 120
maszyn wyeksportowano do krajów zachodnich – głównie:
Włochy, Anglia, RFN, Turcja, Syria, Argentyna, USA
W podziale na typy:
– wiertarko-frezarki – WFB-80 33 szt.
– wiertarko-frezarki – WHB-150 4 szt.
– wiertarko-frezarki-ADS-115 12 szt.
– wiertarko-frezarki – ADP-115 6 szt.
– wiertarko-frezarki – HWCS-110 2 szt.
– tokarki karuzelowe – KNA-110/135 A 40 szt.
– tokarki karuzelowe – KNA-110/135 A (wersja amerykańska)..14 szt.
– stoły obrotowe – S-1600 9 szt.
Szkoła pracownicza
DEFUM posiadało własną szkołę pracowniczą.
Początkowo przed wojną nowi pracownicy szkolili się odbywając 4 letnią, słabo płatną praktykę zakończoną otrzymaniem zaświadczenia.
W erze PRL-u na samym początku wysyłano pracowników na przeszkolenie do Technikum w Bytomiu. Potem jednak utworzono własną szkołę przy ulicy Bolesława Limanowskiego 24. Otwarto ją 3 września 1946 roku. Pierwszym dyrektorem został Mieczysław Skarbek. Na początku szkoła posiadała 110 uczniów w dwóch klasach pierwszych i w jednej drugiej.
Rok szkolny 1947/48 przyniósł dwie klasy pierwsze, dwie klasy drugie i jedną trzecią przy licznie 178 uczniów. Od początku roku szkolnego dyrektorem był Józef Kwiatkowski, a od kwietnia Tadeusz Rączka. Wtedy też zaczęły się pierwsze egzaminy czeladnicze które ukończyło 22 uczniów.
W roku 1948/49 dyrektorem został Mikołaj Orłowski a liczba uczniów wyniosła 228 osób. Trzy dni nauki odbywały się w szkole, w prywatnym, nieprzystosowanym budynku, a kolejne trzy dni w warsztatach szkolnych na terenie fabryki - dziś już nie istniejące - stały w miejscu dawnego targowiska, dziś parkingu WSB. Personel nauczycieli składał się z 12 osób, z czego 7 osób to byli nauczyciele zawodu a reszta dochodząca.
W późniejszym okresie, w latach 70-tych szkoła przeniosła się na ulicę Łańcuckiego, do obecnego pawilonu "B" Technicznych Zakładów Naukowych. Jej pełna nazwa wówczas brzmiała "Technikum dla pracujących Dąbrowskiej Fabryki Obrabiarek Defum , Huty im F. Dzierżyńskiego i Huty Katowice". Zajęcia odbywały się w godzinach popołudniowych i wieczornych, a klasy były podzielone na "huciane" i "defumowskie". Program nauczania był dość spójny z resztą techników w Polsce, lecz nauczyciele mieli możliwość lekkich modyfikacji treści wskazanych dla danego zakładu pracy przy przedmiotach zawodowych. W klasach defumowskich były wprowadzone elementy budowy i programowania obrabiarek sterowanych numerycznie. Wśród nauczycieli znalazły się takie osoby jak Tomasz Derda, Tadeusz Białas , Zdzisław Flak, Jan Wiaderek, Helena Wiaderek. W tym samym budynku w godzinach dopołudniowych działa Zasadnicza Szkoła Zawodowa sponsorowana prze te same fabryki. Szkoła współpracowała z warsztatami szkolnymi DEFUM które posiadały własną hale , a także wyposażenie maszynowe niezbędne do szkolenia uczniów w zawodzie tokarzy ,frezerów, ślusarzy i w innych zawodach przemysłowych. Uczniowie którzy odbywali praktyczna naukę zawodu w warsztatach szkolnych Defum uzyskiwali status pracownika młodocianego. Same warsztaty szkolne były wydziałem produkcyjnym fabryki , nazywanym w strukturach organizacyjnych jako P5. Produkowane przez uczniów proste części były wykorzystywane na zakładzie. Tym sposobem Defum co roku dostawał nowych pracowników . Znaczna część następnie kontynuowała naukę w technikum. W latach siedemdziesiątych dyrektorem szkoły był Stanisław Koziorowski ,a zastępcami J. Kalużny i A.Gębczyński. Wtedy na potrzeby szkoły, fabryki sponsorujące podjęły budowę internatu przy ul .Granicznej. Zmiany w Oświacie spowodowały ,że budynek ten nigdy nie został ukończony zgodnie ze swoim pierwotnym celem, natomiast na końcowym etapie przemianowano go w blok mieszkalny.
Autorzy tekstu: Tomasz Derda oraz Krzysztof Kulik
Źródła:
http://dabrowagornicza.naszemiasto.pl/artykul/przedstawiciele-ponar-defum-w-urzedzie-wojewodzkim,799204,art,t,id,tm.html
http://dabrowagornicza.naszemiasto.pl/artykul/dabrowski-defum-coraz-blizej-upadku,790586,art,t,id,tm.html
http://dabrowagornicza.naszemiasto.pl/artykul/ponar-defum-ma-juz-21-mln-zl-dlugu,803236,artgal,t,id,tm.html
http://dabrowagornicza.naszemiasto.pl/artykul/decyzja-w-rekach-komornika,393512,art,t,id,tm.html
http://dabrowagornicza.naszemiasto.pl/artykul/pracownicy-ponar-defum-pikieta-chca-ratowac-swoje-miejsca,360916,art,t,id,tm.html
http://dabrowagornicza.naszemiasto.pl/artykul/w-ponar-defum-czekaja-na-decyzje-wierzycieli,377834,art,t,id,tm.html
Powiązane artykuły
- Kopalnie, huty, firmy - Zakłady przemysłowe - Defum
- Kolekcje, zbiory, prywatne archiwa - Urząd Miejski w Dąbrowie Górniczej
- Kolekcje, zbiory, prywatne archiwa - Tomasz Derda
- Archiwalia - Dokumenty - Kwestionariusz zdolności produkcyjnych Defum 1934 rok
- Archiwalia - Dokumenty - Kwestionariusz zdolności produkcyjnych Defum 1937 rok
- Archiwalia - Produkty z Dąbrowy - Obrabiarki z DEFUM
- Kolekcje, zbiory, prywatne archiwa - Bernard Jaskuła
- Kolekcje, zbiory, prywatne archiwa - Jacek Zommer
- Archiwalia - Pamiątki z Dąbrowy Górniczej - Firmowe - DEFUM
- Kolekcje, zbiory, prywatne archiwa - Dariusz W. Nelle
Wyszukiwaniew naszej bazie
Nawiguj klikając na trójkąty poniżej
♦ - wpis encyklopedyczny
- Archiwalia
- Bilety
- Dokumenty
- Fotografie
- Koperty
- Mapy
- Odznaki i medale
- Pamiątki z Dąbrowy Górniczej
- Plany
- Pocztówki
- Pozostałe
- Produkty z Dąbrowy
- DELAM
- Huta Szkła Artystycznego Staszic
- Huta Szkła Gospodarczego Ząbkowice
- Motoryzacja
- Obrabiarki z DEFUM
- Centrum obróbkowe wiertarsko-frezerskie WFE 100 NM
- Centrum obróbkowe wiertarsko-frezerskie WFG-100 NM
- Ciężka wiertarko-frezarka ADP-115
- Tokarka karuzelowa KNA -110/135 A
- Tokarka karuzelowa KNA -110/135 B
- Tokarka karuzelowa KNA -110/135 N
- Tokarka karuzelowa KNA -140/160
- WFM-100 N i WFM-100 NM
- Wiertarko-frezarka AD-100 AD-115 AD-125
- Wiertarko-frezarka HWC-P 110A
- Wiertarko-frezarka HWC-S 110A
- Wiertarko-frezarka konwencjonalna ADS-115
- Wiertarko-frezarka WFB-80
- Wiertarko-frezarka WFB-80 S
- Wiertarko-frezarka WFC – 90
- Wiertarko-frezarka WFE – 100 A1 N
- Wiertarko-frezarka WFG-100
- Wiertarko-frezarka WFG-100 N
- Wiertarko-frezarka WHB – 150
- Wiertarko-frezarka WHC – 160
- Wiertarko-frezarki poprzeczne WFE 100 A7 i WFE 100 A9
- Wiertarko-frezarki WFE – 80 i WFE 100
- Wiertarko-frezarki WFM-100
- Reklamy
- Ryciny
- Stemple i pieczątki
- Szkice,plany,projekty
- Tabliczki z dawnymi ulicami
- Tarcze szkolne
- Zaproszenia
- Bibliografia
- Archiwum Państwowe Katowice
- Czasopisma i gazety
- "Przemysł Chemiczny"
- Architektura
- Biesiada Literacka
- Dębowy Puls Miasta
- Dzień Dobry
- Dziennik Częstochowski
- Dziennik Ustaw
- Dziennik Zachodni
- Dzwonek Częstochowski
- Expres Zagłębia
- Gazeta Kielecka
- Gazeta Lwowska
- Gazeta Świąteczna
- Głos Zagłębia
- Głos Ziemowida
- Goniec Częstochowski
- Ilustrowany Kuryer Codzienny
- Innowacyjne obrabiarki – DEFUM 2004
- Iskra
- Jednodniówki
- Jlustracja Polska
- Kino
- Kłosy
- Kolejowe Przysposobienie Kolejowe
- Kurier Codzienny
- Kurier Poranny
- Kurjer Warszawski
- Kurjer Zachodni
- Kuryer Literacko-Naukowy
- Młodzi Idą
- Mówią wieki – magazyn historyczny
- Na szerokim świecie
- New Poland
- Niedziela
- Nowa Reforma
- Nowiny Illustrowane
- Nowości Ilustrowane
- Panorama
- Pobudka
- Polonia **
- Przegląd Dąbrowski
- Przegląd Górniczo-Hutniczy
- Przegląd pożarniczy
- Przegląd Techniczny
- Przekrój
- Przemysłowo-Handlowy Kurjer Sosnowiecki
- Przewodnik Katolicki
- Rola
- Rozwój
- Siedem groszy
- Świat
- Światowid
- Tajny detektyw
- Trybuna Robotnicza
- Turysta
- Tygodnik Ilustrowany
- Tygodnik Powszechny
- Wędrowiec
- Wiadomości Częstochowskie
- Wiadomości polskie
- Wieczór
- Ziarno
- Ziemia
- Dabrowa Gornicza Yizkor Book
- Foldery i broszury
- Katalogi
- Książki i albumy
- "Opis drogi żelaznej Iwangrodzko-Dąbrowskiej"
- Album "Barbórka 1972"
- Album Dąbrowa Górnicza
- Album drużyny harcerskiej im. Kr. Jana Sobieskiego
- Album p. Czesława Marczewskiego
- Album z czasów okupacji
- Dąbrowa Górnicza – rozwój urbanistyczny miasta
- Geografia powszechna illustrowana
- Geologiczny opis Polski oraz innych krajów, na północ od Karpat położonych
- Huta Katowice – stan oblężenia
- Ilustrowany Przewodnik Kolejowy
- Królestwo Polskie
- Książka telefoniczna o okręgu krakowskiego i Zagłębia Dąbrowskiego z 1929
- Legenda Zagłębia
- Legendy Zagłębia
- Monografia Dąbrowy Górniczej – 1976
- Monografia Huty Bankowej
- Słownik Geograficzny Królestwa Polskiego
- Spółdzielczość w Dąbrowie Górniczej 1886-1966
- Sprawozdanie z ogólnopolskiego zjazdu w sprawach komunikacji miejscowej
- Syn Człowieczy
- V zjazd absolwentów Szkoły Górniczej i Hutniczej oraz Technikum Górniczego
- Wspólnymi siłami – X lat FOS
- Wspólnymi siłami – X lat Funduszu Odbudowy Szkół
- Wycieczki jednodniowe Zagłębia
- Yizkor Book – Dabrowa Gornicza
- Z biegiem Wisły
- Z biegiem Wisły. Obrazki o kraju.
- Z przeszłości Zagłębia Dąbrowskiego i okolicy
- Zagłębie Dąbrowskie – Jan Zieliński
- Zarys dziejów hutnictwa i naukowo-technicznych stowarzyszeń hutniczych
- Ziemia Rodzinna
- Żydzi na Górnym Śląsku i w Zagłębiu Dąbrowskim
- Księgi adresowe i telefoniczne
- Adressbuch 1914-1915
- Chrześcijański Informator Zagłębia Dąbrowskiego na rok 1938
- Kalendarz Wieku Illustrowany
- Księga adresowa przemysłu, handlu i finansów – 1922
- Rocznik adresowy Królestwa Polskiego – 1900
- Rocznik adresowy Królestwa Polskiego – 1902
- Spis abonentów sieci telefonicznych Dyrekcji Okręgu Poczt i Telegrafów w Katowicach na 1939
- Księgi pamiątkowe
- Zasoby internetowe
- architekt.bedzin.pl
- Archiwum Map Zachodniej Polski
- Archiwum strony internetowej Cutiron
- Biblioteka Jagiellońska
- Biblioteka Narodowa
- Dolnośląska Biblioteka Cyfrowa
- Forum Klimontów-Sosnowiec
- Fototeka Filmoteki Narodowej
- mapywig.org
- Narodowe Archiwum Cyfrowe
- naszgolonog.net
- Polona
- Portal aukcyjny
- rcin.org.pl
- Śląska Biblioteka Cyfrowa
- Stare Bilety PKP
- Tadnum – portal aukcyjny
- Wikipedia – domena publiczna
- www.antoniow.dbv.pl
- www.jewishgen.org
- zabytki.pl
- zdpp.blogspot.com
- Dzielnice
- Aleje
- Antoniów
- Błędów
- Bugaj
- Centrum
- 3 Maja
- Aleja Róż
- Aleja Tadeusza Kościuszki
- Bolesława Limanowskiego
- Budynek ekspedycji kopalni "Reden"
- Dzielnice
- Elizy Orzeszkowej
- Feliksa Perla
- Górnicza
- Górników Redenu
- Henryka Dąbrowskiego
- Henryka Sienkiewicza
- Hugona Kołłątaja
- Jana III Sobieskiego
- Juliusza Kadena-Bandrowskiego
- Kolejowa
- Królowej Jadwigi
- Księdza Augustynika
- Legionów Polskich
- Marii Konopnickiej
- Mikołaja Kopernika
- Nieznana ulica
- Nowa
- Ogrodowa
- Paryska
- Plac lotnika Żwirki
- Plac lotnika Żwirki
- Plac Wolności
- Romualda Traugutta
- Siemońska
- Stefana Okrzei
- Stefana Żeromskiego
- Władysława Przybylaka
- Zygmunta Cieplaka
- Dębniki
- Do identyfikacji
- Dziewiąty, Jedenasty, Trzydziesty, Szósty
- Gołonóg
- Adama Mickiewicza
- Aleja Józefa Piłsudskiego
- Aleja Zagłębia Dąbrowskiego
- Bolesława Prusa
- Edmunda Cedlera
- Generała Józefa Bema
- Gwardii Ludowej
- III Powstania Śląskiego
- Józefa Wybickiego
- Kościelna
- Kosmonautów
- Laski
- Marcina Kasprzaka
- Nieznana ulica
- Parkowa
- Plac Waszyngtona
- Romana Piecucha
- Tysiąclecia
- Walentyny Tiereszkowej
- Wiśniowa (nieistniejąca)
- Jamki
- Jedenasty
- Kasprzak
- Kazdębie
- Korzeniec
- Koszelew
- Ksawera
- Łabęcka
- Łęka
- Łęknice
- Łosień
- Manhattan
- Morcinek
- Mydlice
- Nieznana dzielnica
- Okradzionów
- Piaski
- Piekło
- Pilicka
- Podlesie
- Pogoria
- Reden
- Sikorka
- Stara Dąbrowa
- Staszic
- Strzemieszyce Małe
- Strzemieszyce Wielkie
- Ciołkowizna
- Fabryczna
- Gabriela Narutowicza
- Hetmańska
- Jana Majewskiego
- Kolejowa
- Kościelna
- Młyn
- Nieznana ulica
- Obrońców Pokoju
- Ofiar Katynia
- Puszkina
- Sławkowska
- Sportowa
- Stacyjna 18
- Strzemieszycka
- Sulno
- Szosowa (Strzem.)
- Tadeusza Gruszczyńskiego
- Transportowa
- Warszawska (wcz. Piłsudskiego)
- Władysława Orkana
- Trzebiesławice
- Tuczna Baba
- Tworzeń
- Ujejsce
- Ząbkowice
- Aleja Zwycięstwa
- Armii Krajowej
- Chemiczna
- Czesław Domaniewski
- Dolomitowa
- Dworcowa
- Franciszka Zabłockiego
- Generała Władysława Sikorskiego
- Górzysta
- Gospodarcza
- Gustawa Dreszera
- Janusza Kusocińskiego
- Młynarska
- Nadrzeczna
- Nieznana ulica
- Odrodzenia
- Orzechowa
- Osiedle Młodych Hutników
- Wapienna
- Zagłębiowska
- Związku Orła Białego
- Zagórze
- Zając
- Zielona
- Edukacja
- Kursy i szkolenia
- Liceum Plastyczne
- Seminarjum Nauczycielskie
- Szkoły
- Gimnazja
- Niezidentyfikowana
- Państwowe Seminarjum Nauczycielskie Męskie im. Traugutta
- Podstawowe i powszechne
- Cheder – szkoła żydowska
- Powszechna Szkoła Publiczna im.Marii Konopnickiej
- Szkoła im. Emilii Zawidzkiej
- Szkoła Kolejowa w Strzemieszycach
- Szkoła Podstawowa nr 1 w Gołonogu
- Szkoła Podstawowa nr 10
- Szkoła Podstawowa nr 12
- Szkoła Podstawowa nr 13 im. Adama Piwowara
- Szkoła Podstawowa nr 15
- Szkoła podstawowa nr 16 imienia Waleriana Łukasińskiego
- Szkoła Podstawowa nr 17
- Szkoła Podstawowa nr 2 (Strzemieszyce)
- Szkoła Podstawowa nr 20
- Szkoła Podstawowa nr 21
- Szkoła Podstawowa nr 22
- Szkoła Podstawowa nr 29 im. Alfreda Szklarskiego
- Szkoła Podstawowa nr 3 im. Adama Mickiewicza
- Szkoła Podstawowa nr 3 im. Mikołaja Kopernika
- Szkoła Podstawowa nr 4 – Łęknice
- Szkoła Podstawowa nr 5 im. Henryka Sienkiewicza
- Szkoła Podstawowa nr 6
- Szkoła Podstawowa nr 7 im. Hugona Kołłątaja
- Szkoła Podstawowa nr 8
- Szkoła w Błędowie
- Ząbkowice – niemiecka szkoła
- Przedszkola
- Średnie i zawodowe
- I LO im. Waleriana Łukasińskiego
- II LO im. Stefana Żeromskiego
- Liceum im. Aleksandra Zawadzkiego
- Szkoła Przemysłowa Śląsko-Dąbrowskiej Fabryki Urządzeń Mechanicznych
- Szkoła przy ul. 3-go Maja 10
- Sztygarka
- Techniczne Zakłady Naukowe
- Zespół Szkół Ekonomicznych im. Karola Adamieckiego
- Zespół Szkół Technicznych
- Szkoła Muzyczna
- Szkoły Specjalne
- Wyższe
- Tarcze szkolne
- Zespół Szkół Sportowych im. Polskich Olimpijczyków
- Żłobki
- Kolekcje, zbiory, prywatne archiwa
- Abraham Stavsky
- Adam Gołębiowski
- Adam Jamrozy
- Adam Tryba
- Adrian Dąbrowski
- Adrian Kretowicz
- Agata Kołodziejczyk
- Agnieszka Bryzik
- Agnieszka Janicka-Kwiecień
- Agnieszka Lisak
- Agnieszka Malawska
- Agnieszka Tabor
- Aleksander Wolski
- Alicja Smolarska
- Alojzy Pacha
- Andrzej Bogusław
- Andrzej Danecki
- Andrzej Grygiel
- Andrzej Grzebielucha
- Andrzej Kontkiewicz
- Andrzej Laskowski
- Andrzej Ludkiewicz
- Andrzej Nowak
- Andrzej Płatek
- Andrzej Tarczewski
- Andrzej Wilewski
- Ania M. Sokołowska
- Anita Dróżdż Lorens
- Anna Borecka
- Anna Borucińska
- Anna Jabłońska
- Anna Neumann
- Anna Pełka
- Anna Syska
- Anna Zugaj
- Antoni Leśniak
- Antykwariat POLIART
- Archiwum Państwowe w Katowicach
- Archiwum Państwowe w Kielcach
- Archiwum Państwowe w Łodzi
- Archiwum rodziny Hoffmanów
- Archiwum Urzędu Miejskiego w Dąbrowie Górniczej
- Arkadiusz Rybak
- Artur Burdasz
- Artur Kamiński
- Barbara Kuzior
- Barbara Szczygieł
- Bart Plucinski
- Bartek
- Bartosz Kaczmara
- Bartosz Maroszek
- Bartosz Rutkowski
- Beata Grabowska
- Bernard Jaskuła
- Bogusław Duda
- Cezary Śliwiński
- Damian Góral
- Daniel Wróblewski
- Daniel Zasimuk
- Daria Wilczyńska-Zięba
- Dariusz Andrzej Kurpiel
- Dariusz Bartnik
- Dariusz Chećko
- Dariusz W. Nelle
- Dariusz Westphal
- Dawid Kmiotek
- Dawid Zegan
- Dominik Szczawiński
- Edward Kaleta
- Edyta i Andrzej Pardała
- Ewa Blacha
- Ewa Kartas
- Ewa Stęplewska
- Famille PRUDENT à Genlis France
- Gabriel Sołtysik
- Gabriela Struzik
- Galeria Akcji
- Grzegorz Kryczka
- Grzegorz Milewski
- Grzegorz Rokicki
- Grzegorz Skwara
- Grzegorz Taubler
- Grzegorz Walnik
- Halina Urban
- Hanna Klapa
- Helena Pentaks
- Henryk Adamczyk
- Henryk Boberek
- Henryk Bryś
- Henryka Kopeć
- Herder-Institut
- Horse Cars – Auto Serwis
- Hufiec ZHP
- Igor Puchała
- Ilona Blecha
- Ireneusz Górny
- Iwona Matyja
- Iwona Sułkowska
- Jacek Bargieł
- Jacek Kułach
- Jacek TZN
- Jacek Walaszczyk
- Jacek Zommer
- Jadwiga Machocka
- Jakub Łazarowicz
- Jakub Zasucha
- Jan Dudek
- Jan Giemza
- Jan Janocha
- Jan Krepa
- Jan Wątrobiński
- Janek Szuba
- Janusz Dziubiński
- Janusz Kurzyński
- Janusz Olej
- Jarosław Haszek
- Jarosław Janik
- Jarosław Krajniewski
- Jarosław Sawicz
- Jarosław Synowiec
- Jeff Cymbler
- Jerzy Sobota
- Joanna i Jerzy Gidmańscy
- Joanna Karlik
- Joanna Kwiecień
- Joanna Wierzbicka-Niechciał
- Jolanta Stolarska
- Jorge Szot
- Józef Makal
- Justyna Jaros Dziub
- Justyna Karwalska
- Justyna Pełechacz
- Kamil Potocki
- Kamil Rakowski
- Kamila Milik
- Kamila Przetak
- Karol Pieróg
- Karolina Kot (szkieletek)
- Katarzyna Bojarska
- Katarzyna Broda
- Katarzyna Grzyb
- Kazimierz Sendek
- Klaudia Budzyńska
- Klub Osiedlowy Unikat
- Konrad Kępski
- Krzysztof Janik
- Krzysztof Janus
- Krzysztof Kucharczyk
- Krzysztof Kulik
- Leszek Lasok
- Leszek Maszczyk
- Lidia Sztur-Majchrzak
- Lidia Wojtek
- Łukasz Bardzyński
- Łukasz Dobrowolski
- Łukasz Jermacz
- Łukasz Kuszniersky
- Łukasz Musiałek
- Łukasz Olejniczak
- Łukasz Pawlik
- Łukasz Tomczyk
- Łukasz Zięba
- Łukasz Zmarzły
- Łukasz Zwoliński
- Maciej Gadaczek
- Maciej Partyka
- Maciej Wróblewski
- Magdalena Bernacka
- Magdalena Grząś
- Magdalena Jasińska
- Magdalena Wawrzyńczak
- Maja Szwedzińska
- Małgorzata Błaut
- Małgorzata Bogusław
- Małgorzata Grażyna Korpikiewicz
- Małgorzata Kamińska
- Małgorzata Kowalczyk
- Małgorzata Lehman
- Marcin Błaszczyk – fotoplant.pl
- Marcin Demski
- Marcin Macha
- Marcin Maślak
- Marcin Michał Macha
- Marcin Mikina
- Marcin Młyński
- Marcin Rokicki
- Marcin Skorek
- Marek Brodnicki
- Marek Karnecki
- Marek Nuckowski
- Marek Słowiński
- Marek Wójcik
- Maria Czajka
- Marian Sauczek
- Mariusz Krakowiński
- Mariusz Nowakowski
- Marta Grzechuła
- Marta Rychlik
- Marta Szczepanik
- Marzena Smok
- Marzena Wiczkowska
- Michał Borchmann
- Michał Chlipała
- Michał Chojkowski
- Michał G.
- Michał Giemza
- Michał Głubiak
- Michał Kocma
- Michał Radka
- Michał Rodacki
- Michał Szczepanik
- Mieszko Opiłka
- Mirosław Stróżycki
- MJK89
- Moniek Rozen
- Monika Korzeniec-Olszewska
- Monika Pluta
- Monika Zawadzka
- Muzeum Krakowa
- Muzeum Miejskie Sztygarka
- Narodowe Archiwum Geologiczne
- New York Library
- Ola Olbrychowska-Ciepły
- Olga Adamus-Świercz
- Olga Kazibudzka
- Österreichisches Staatsarchiv w Wiedniu
- p. Juliusz
- Państwowy Instytut Geologiczny
- Patrick Chlond
- Patrycja Kordyś
- Patryk Chorążewicz
- Patryk Jeliński
- Patryk Nowakowski
- Paulina Gajewska
- Paweł Dydak
- Paweł Fałda
- Paweł Pudlik
- Paweł Smalcerz
- Piotr Frączak
- Piotr Gawor
- Piotr H.
- Piotr Kołodziejczyk
- Piotr Kozłowski
- Piotr Szafarz
- Piotr Wątrubka
- Piotr Zach
- Przemysław Kowalski
- Przemysław Woźniak
- Rafał Bujakowski
- Rafał Gawęda
- Rafał Kwieciński
- Rafał Piętka
- rcin.org.pl
- Robert Altman
- Robert Bączek
- Robert Kośmider
- Robert Kudera
- Robert Ochocki
- Robert Strojek
- Robert Winkler
- Rodzinny zbiór Państwa Bączek
- Rodzinny zbiór Państwa Dulewskich
- Rodzinny zbiór Państwa Karnasiewicz
- Rodzinny zbiór Państwa Rogacz
- Rodzinny zbiór Państwa Strasz
- Roman Kidller
- Roman Malik
- Ryszard Siewniak
- Ryszard Sokół
- Sebastian Glonek
- Sławek Kartonik
- Stanisław Małyska
- Stanisław Pancesz
- Stanisław Szpruch
- Sylwester Dominik
- Szymon Hnatow
- Szymon Lubaszka
- Tadeusz Iwoński
- Tadeusz Lorenc
- Tomasz Byjos
- Tomasz Derda
- Tomasz Grzegorz
- Tomasz Ruciński
- Tomasz Szymczyk
- Tomasz Zamysłowski
- Tomek S.
- Tymek Skrzelowski
- United States Holocaust Memorial Museum (USHMM)
- Urszula Ostrowska
- Urząd Miejski w Dąbrowie Górniczej
- Veteran Club 1978 – Dąbrowa Górnicza
- Violetta Piątek
- Waldemar Magnuszewski
- Wiesław Duda
- Wiesław Trzęsimiech
- Witold Molęda
- Witold Wieczorek
- Włodzimierz Starościak
- Wojciech Bański
- Wojciech Kozina
- Wojciech Morawiec
- Wydawnictwo DIKAPPA
- Yestersen
- Zbieracz Staroci
- Zbigniew Bartnik
- Zbigniew Kornet
- Zbigniew Myśliński
- Zenon Zacłon
- Zofia Budziarz
- Kopalnie, huty, firmy
- Banki
- Bary
- Cegielnie
- Domy i centra handlowe
- Dyskoteki
- Firmy,biura,przedsiębiorcy
- A. Kałkowski, K. Zieliński i S-ka
- Biuro Budowlane Edward Kosiński
- Biuro Budowlane W. Wojewódzkiego
- Biuro Techniczne Inż. A. Nowicki
- Elibor
- Fabryka Gilz Stefan Serrini
- Fabryka kartonów i opakowań
- Galanteria "Izydor"
- Guttman – skup mat. drzewnych
- Hurtownia Chrześcijańskiego Towarzystwa Dobroczynności
- Jan Dąbrowski Biuro Handlowo-Przemysłowe
- K. Kostrzeński
- Magazyn galanteryjno-bławatny R. Rudzki
- Nauczycielka Śpiewu L. Koźminówna
- OPEC
- OSK Efekt
- Przedsiębiorstwo Robót Ciesielskich O. Lange
- Przemysł drzewny I. M Wajnsztajn
- Skład Manufaktury Icek Ugner
- Skład Materiałów Aptecznych Z. Jackowski
- Skład Mebli Jakób Mitelman
- Skład S. Moneta i S-ka
- Spółdzielnia Delam
- Spółdzielnia Inwalidów im. M. Fornalskiej
- Spółdzielnia Pracy "Stolmet"
- Spółdzielnia Rzemieślnicza Remet
- Spółka Leśna Zagłębia Dąbrowskiego
- Sprzedaż drzewa CH. Taub
- Sprzedaż drzewa G. Nussbaum
- Tartak "Janina"
- Tartak i Heblarnia
- Towarzystwo Franko-Polskie
- W. Kozłowski i A. Kalkowski
- Weterynarze
- Zakład Fryzjerski Kremblewskiego
- Zakład pogrzebowy przy ul. 3-go Maja 10a
- Zakłady Schlenck
- Fotografowie
- A. Brodecki
- Arnold Vielrose
- Bogdan Szubski
- Bracia Altman
- Brodecka i Motz
- Cecylia Majewska
- Dariusz Kmiotek
- Dawid Zegan
- Dikappa
- DX FOTO
- E. Furman
- E. Katolik
- Franciszek Stobik
- J. Brodecka
- J. Czachowski
- J. Rowiński
- J. Żelichowski
- Józef Makal
- K. Jabłoński
- K. Kaczyński
- Kazimierz Seko
- Koło fotograficzne Sztygarki
- Krzysztof Kulik
- Laboratorium Fotograficzne przy kopalni "Paryż"
- Leszek Maszczyk
- M. Arbus
- Marcin Nowak
- Marie Putner
- Mieczysław Torbus
- Orient
- P. Pasek
- R. Altman
- R. Brandys
- R. Gwiazda
- R. Radzikowski
- Ryszard Rusak
- Spółdzielnia Pracy Fotografów Zawodowych
- St. Karpenstein
- T. Hermańczyk
- VENUS
- W. Kwietniewski
- Wojciech Bański
- Hotele
- Huty
- Kamieniołomy i wapienniki
- Kopalnie
- Aleksander
- Aleksandra
- Baśka
- Biedaszybownictwo
- Cieszkowski
- Flora
- Hieronim
- Ignacy
- Jan
- Karol
- Kołłątaj
- Kopalnia piasku Kuźnica Warężyńska
- Koszelew
- Ksawery
- Lech
- Łabecki
- Maksymiljan II
- Mikołaj
- Niezidentyfikowana
- Paryż
- Podreden
- Reden
- Schuman
- Sobiesław
- Stanisław
- Sztolnia ćwiczebna
- Szyb nr 34
- Szyb wodny
- Victoria
- Wańczyków
- Wanda
- Wiesława
- Wiktorja
- Zdzisław
- Księgarnie, drukarnie, introligatornie, redakcje gazet
- Dom Książki
- Drukarnia "Górnik"
- Drukarnia i introligatornia "Sztuka"
- Drukarnia St. Święckiego
- Introligatornia Pawła Śmielewskiego
- Księgarnia J. Ringmana
- Księgarnia Jana Rowińskiego
- Księgarnia Kostrzeńskiego
- Księgarnia L. Ciągała
- Księgarnia Leokadji Ottowej
- Księgarnia Ludowa
- Księgarnia ST. Kryszyńskiej w Strzemieszycach
- Księgarnia Żmigroda
- Wypożyczalnia książek C. Kozłowskiej
- Wypożyczalnia książek na Redenie
- Wypożyczalnia książek W. Kaznowskiego
- Zakład poligraficzny "Offset"
- Lody z pianką – p. Szotowa (Wera)
- Młyny
- Ośrodki wypoczynkowe
- Poczta
- Przedsiębiorstwa rolnicze – PGR-y GS-y Samopomoc Chłopska
- Restauracje
- Adria
- Astoria
- Bar u Janka Zawrata
- Cukiernia i Restauracja Wincenty Pietrzak
- Cukiernia Sielanka
- Cukiernia Warszawska S. Burchard
- Diament
- Hubertus
- Karczma w Bugaju (nieistniejąca)
- Kawiarnia "Kaprys" na Gołonogu
- Kawiarnia Gruzińska
- Kawiarnia w hotelu Zagłębia
- Klub Górniczy ZRPME PW Damel
- Kolorowa
- Mc Donald
- Niezidentyfikowana
- Parkowa
- Restauracja Chińska
- Restauracja POLONIA
- Restauracja R. Hajkiewicz
- Restauracja Stefana Wilczyńskiego
- Stylowa
- Tel-aviv
- Z. Sifijanowski
- Zacisze
- Zagłębianka
- Rzemieślnicy
- A. Miodownik
- Erato – wytwórnia strun (w Hubertusie)
- Idzi Lorens – fryzjer
- Krawiec Kanarek
- Niezidentyfikowany malarz
- Pracownia obuwia Leon Kasperek
- Przeds. Leśne – M. Gąssowski
- Salon fryzjerski Józefa Sauczka
- Stefan Pawłowski – mistrz fryzjerski
- Warsztat blacharski B. Lajtnera
- Wyrób butów
- Wyrób instrumentów muzycznych Jan Wilkoszewski
- Zakład Fryzjerski – Alojzy Pacha
- Zakład jubilersko-zegarmistrzowski J. Bocianowski i Syn
- Zakład kamieniarski "Wiktorja "
- Zakład kamieniarski Fochtmana
- Sklepy
- Antykwariat "Argos"
- Aparaty radiowe, gramofony J. Schabowski
- Apteka Grochowskiego
- Apteka Panaceum
- Artykuły Metalowe na 3 maja
- Bambosz
- Barbara – hurtownia krawiecka
- Chrześcijański dom obuwia ludowego
- Cliff Kosmetyki
- Drogeria na 3 maja
- Eldom
- Elegancja
- Foto DX
- Fryzjer Mieczysław Ziomek
- Galanteria Józef Paluchiewicz
- Kiosk na rogu 3 Maja
- Kioski Ruch-u
- Konalina Sklep Firmowy
- Kwiaciarnia i owocarnia "Araukaria"
- Magazyn Konfekcji G. Moszkowicz
- Magazyn mody H. Kossobudzkiej
- Magazyn Nadzieja
- Magazyn obuwia M. Rzepecki
- Nastolatek
- Niemiecki sklep na Redenie
- Niezidentyfikowane
- Optyk na 3 maja
- Pasmanteria
- Pewex
- Produkcja i Sprzedaż Farb Zyndel Szancer
- Radio i Technika
- Radio Telewizja
- Robot
- Rzeczki-złoto, srebro,zegary
- Sklep "Alik"
- Sklep galanteryjny C. Smolarska
- Sklep Mazurkiewicza
- Sklep niemiecki Lebensmittel
- Sklep Sołtysika na Redenie
- Sklep Stowarzyszenia Robotników Chrześcijańskich
- Sklep z chemią na Bandrowskiego
- Sklep z odzieżą na Sienkiewicza
- Sklepy "Społem"
- Sklepy pod Sobieskiego 4
- Skład Apteczny Jan Beranek
- Skład Apteczny S-rów Jana Grochowskiego
- Supermarkety PRL-u
- Tkaniny Dekoracyjne
- Uniwersal
- Sklepy i przemysł spożywczy
- Cerealia oddział w Dąbrowie
- Cukiernia "Wersal"
- Delikatesy w Merkurym
- Handel win, wódek i towarów kolonialnych Emil Woźniak
- Hurtownia Cukru Mieczysław Dyja
- Icek Fraiman, W. Fraiman – reprezentacja browaru
- Kiosk spożywczy na Redenie Karnieckich
- Mięsny w Gołonogu
- Pieczywo i nabiał na Gołonogu
- Rzeźnia miejska
- SAM w Merkurym
- Sklep Grudnika
- Sklep spożywczo-kolonialny wyroby tytoniowe i manufaktury H. Kotuła
- Sklep spożywczy i elektryczna palarnia kawy Jan Domagała
- Sklep spożywczy robotników kopalni "Flora"
- Skład Ryżu i Cukru J. Rozenberg i S-ka
- Skład Win i Delikatesów Stefan Wilczyński
- Sprzedaż mąki i kaszy B-cia D. i Sz. Silberfreund
- Sprzedaż mąki i kaszy I. Welner
- Sprzedaż Mąki i Zboża J. Edelist i L. Welner
- Sprzedaż Wyrobów Cukierniczych
- Wytwórnia Wód Gazowanych
- Wytwórnia Wód Gazowo-Owocowych Fr. Żaka
- Wytwórnia Ziół Leczniczych ks. Huszno
- Targowiska
- Wieże wodne
- Zakłady przemysłowe
- Betoniarnia w centrum
- Dąbrowskie Zakłady Chemiczne i Fabryka Tektury Asfaltowej
- Dąbrowskie Zakłady Przemysłu Terenowego
- Damel
- Defum
- Elektryczność / ERG
- Fabryka Drutu Braci Klein
- Fabryka forniru
- Fabryka Mydła "Alfa"
- Fabryka Mydła "Dzwon"
- Fabryka przetworów chemicznych – W. Mondalski
- Fabryka Śrub i Nitów
- Fabryka zamków i okuć "Tłocznia"
- HK Cutiron
- Huta Szklana "Strzemieszyce"
- Huta Szkła Artystycznego Staszic
- Huta Szkła Ząbkowice
- IZOKOR
- Koksownia "Przyjaźń"
- Odlewnia Wszelkich Metali Bolesław Plucinski
- Strem
- Wibrobeton
- Zakład Ślusarko-mechaniczny Teofil Brok
- Zakłady Bytomskie
- Zakłady Mechaniczne Władysława Pająka
- Zakłady Naprawcze Maszyn Elektrycznych
- Zakłady przemysłowe "Strzemieszyce"
- Zakłady Tworzyw Sztucznych Ząbkowice
- Kultura
- Nieskategoryzowane
- Obiekty wojskowe
- Osoby
- A. Miodownik
- Abram Jakub Klein
- Andrzej Ornat
- Andrzej Rosicki
- Antoni Kozioł
- Antoni Pinkowski
- Artyści
- Bolesław Zarychta
- Bronisława Kmiecik
- Budowniczy miasta
- Czesław Rabenda
- Dąbrowska inteligencja – międzywojnie
- Edward Bryła
- Edward Miętka
- Edward Salwa
- Eryka Trzewik-Drost
- Eugeniusz Furman
- Eugeniusz Jarubasz
- Franciszek Szklaz
- Goście Dąbrowy
- Grzegorz Borowiec
- Henryk Kanwiszer
- Hieronim Kondratowicz
- Hieronim Uczyński
- Ireneusz Borowiec
- Jan Kruszyński
- Jan Sylwester Drost
- Jan Tyka
- Józef Chlebowski
- Józef Piątek
- Józef Starzyński
- Julian Hoffman
- Kazimierz Srokowski
- Leon Juszczyk
- Leszek Rozmus
- Ludwik Fiedorowicz
- Maria Piętkówna
- Maria Szklaz
- Marian Kantor-Mirski
- Marian Sowiński
- Mieszkańcy
- Adolf Kowalski
- Antoni Zawodniak
- Augustynik Grzegorz – ksiądz
- Bolesław Sierka
- Eugeniusz Smirnow
- Ferdynand Peroń
- Franciszek Latała
- Franciszek Łach
- Franciszek Wilkoszewski
- Francuzi
- Janek Boruszewski
- Janina Starzyńska
- Kazimierz Bargieł
- Kazimierz Morgulec
- Kazimierz Wilkoszewski
- Maciej Dalewski
- Maria Zawodniak
- Maryanna Świerczewska
- Podkowa Aniela
- Rodzina Śmielewskich
- Stanisława Sauczek
- Stefan Czajkowski
- Szczepan Słowiński
- Tadeusz Jaworski – architekt
- Tadeusz Szymaszek
- Teofil Wójcik
- Tomasz Lubojański
- Wacława Sonne
- Weronika Karnecka
- Włodzimierz Starościak
- Zdanowska Joanna
- Zygmunt Wydrych
- Nauczyciele
- Piotr Reroń
- Piotr Urbańczyk
- Politycy
- Przedsiębiorcy, właściciele sklepów
- Przemysł
- Rodzina Domańskich
- Rodzina Gęborków
- Rozalia Smółkowa
- Stanisław Janas
- Stanisław Kontkiewicz
- Stanisław Lewiński
- Stanisław Siudak
- Stanisław Sobieraj
- Stanisław Wiewióra
- Uczniowie
- Wł. Liwierski
- Władysław Bubel
- Władysław Dziurski
- Władysław Mogiła
- Wojskowi
- Zdzisław Sikora
- Zenon Wojtala
- Żydzi
- Zygmunt Bąbczyński
- Zygmunt Ciuk
- Zygmunt Sztainmasel
- Pomniki i tablice
- Bohaterom Czerwonej Armii ("gwiazda") – Gołonóg
- Figura Maryi przed Bazyliką NMP
- Figura Maryi z boku Bazyliki NMP
- Instalacja przy CH Merkury
- Pomnik 10 zamordowanych
- Pomnik Aleksandra Zawadzkiego
- Pomnik Bohaterów Czerwonych Sztandarów (Hendrix)
- Pomnik Feliksa Dierżyńskiego
- Pomnik Legionistów (nieistniejący)
- Pomnik Niepodległości
- Pomnik Nieznanego Żołnierza(wyburzony)
- Pomnik Stanisława Staszica
- Pomnik Tadeusza Kościuszki
- Pomnik Tadeusza Kościuszki na Placu lotnika Żwirki (nieistniejący)
- Pomnik z menorą na kirkucie
- Pomnik Żołnierzy Radzieckich
- Pomnik Związku Orła Białego
- Tablica – zbiornik Pogoria
- Tablica upamiętniająca E. Furmana
- Tablica upamiętniająca Feliksa Dzierżyńskiego
- Religia
- Cmentarze
- Judaika
- Kapliczki
- Kościoły rzymskokatolickie
- Bazylika Najświętszego Serca Pana Jezusa
- Bazylika NMP Anielskiej
- Kościół Ducha Św.
- Kościół Najświętszej Maryi Panny Królowej Polski
- Kościół Podwyższenia Krzyża Świętego w Łośniu
- Kościół pw. Chrystusa Króla
- Kościół pw. św. Marii Magdaleny
- Kościół pw. św. Rafała Kalinowskiego
- Kościół pw. Trójcy Przenajświętszej
- Kościół św. Aleksandra
- Kościół św. Antoniego z Padwy
- Kościół św. Barbary
- Kościół św. Józefa
- Kościół św. Maksymiliana Kolbego
- Kościół w Ujejscu pw. NMP Matki Kościoła
- Kościół Zesłania Ducha Świętego w Ząbkowicach
- Krzyże przydrożne, okolicznościowe, symboliczne itd
- Księża i siostry zakonne
- Relikty przeszłości
- Służby
- Sport
- Tablice edukacyjne – MMS
- Towarzystwa, stowarzyszenia, harcerze
- Cechy rzemieślnicze
- Dąbrowskie Towarzystwo Muzyczne
- Harcerze
- Koło Gospodyń Wiejskich Strzemieszyce
- Organizacje związkowe
- Partie polityczne
- Spółdzielnie
- Stowarzyszenia
- Hashomer Hatzair
- Koło Samopomocy Uczniów Państwowego Seminarjum Nauczycielskiego
- Liga Kobiet
- Liga Morska i Kolonialna
- NSZZ Solidarność DFO
- Ochronka na Zielonej
- Samowar
- Stowarzyszenie Krzewienia Kultury Fizycznej
- Stowarzyszenie Młodzieży Polskiej
- Stowarzyszenie Młodzieży Żeńskiej
- Stowarzyszenie Robotników Chrześcijańskich
- Stowarzyszenie Spożywców Robotników Chrześcijańskich
- Stowarzyszenie Spożywcze Flora
- Stowarzyszenie spożywcze robotników Huty Bankowej
- T.U.R.
- VC 19-78 MC Poland
- Zespół zwolenników sceny Polskiej
- Związek byłych Ochotników Armji Polskiej
- Związek Nauczycielstwa Szkół Powszechnych Ognisko w Dąbrowie Górniczej
- Związek Orła Białego
- Związek Zawodowy Robotników Przemysłu Górniczego
- Stowarzyszenie pań św. Wincentego
- Towarzystwa
- Duszpasterstwo Ludzi Pracy
- Koło Towarzystwa Macierzy Szkolnej
- Komitet Opieki nad biednymi
- Komitet Opieki nad Dziećmi
- Komitet Ratunkowy miejscowy
- L.O.P.P.
- Obwodowy Komitet Ratunkowy
- PTTK
- Sekcja Górniczo-Hutnicza
- Sekcja VII górniczo hutnicza Towarzystwa popierania przemysłu i handlu
- Sokół
- Stowarzyszenie Robotników Chrześcijańskich
- Towarzystwo "Dobroczynność" kopalni "Flora"
- Towarzystwo Dobroczynności
- Towarzystwo Francusko-Włoskie Dąbrowskich Kopalń Węgla
- Towarzystwo Koło Sportowe
- Towarzystwo Muzyczne w Dąbrowie
- Towarzystwo Muzyczno-Śpiewacze w Gołonogu "Harmonja"
- Towarzystwo pomocy dla biednych chrześcijan kopalni "Flora"
- Towarzystwo poszukiwaczy skarbów
- Towarzystwo Przyjaźni Polsko-Radzieckiej
- Towarzystwo Stenografów Adama Piwowara
- Towarzystwo Upiększania Miasta Dąbrowa Górnicza
- Towarzystwo Wzajemnego Kredytu
- Ubezpieczalnia Społeczna
- Wolny Związek Zawodowy
- Związek Młodzieży Polskiej
- Związek Niemieckich Dziewcząt
- Transport i komunikacja
- Uroczystości i wydarzenia
- 1966 – wizyta Stanisławy Zawadzkiej
- Auto-Rodeo
- Barbórki
- Cyrk
- Dni Dąbrowy Górniczej
- Dożynki
- Dzień Hutnika
- Dzień Znaczka Pocztowego
- Festiwale, imprezy
- Harcerskie
- Jarmark Staroci
- Jubileusze
- Katastrofy, pożary, wypadki
- Kościelne
- Obchody św. Mikołaja
- Obrona pomnika Bohaterów Czerwonych Sztandarów (Hendrixa)
- Odsłonięcie pomnika "Bohaterom czerwonych sztandarów"
- Odsłonięcie pomnika Aleksandra Zawadzkiego
- Otwarcia
- Otwarcie ośrodka zdrowia z E. Gierkiem
- Otwarcie szkoły SP29
- Parady wojskowe
- Partyjne
- Pogrzeby
- Powitanie gauleitera Śląska Fritza Brachta
- Protesty
- Przywitanie rumuńskich przesiedleńców
- Sesje astronomiczne, obserwacje słońca
- Sportowe
- Spotkania i zloty
- Strajki
- Święta Narodowe
- Święto Ameryki Północnej
- Szkolne
- Sztandar dla strażaków z Trzebiesławic
- Targi, kiermasze, jarmarki
- Wojewódzki Przegląd Piosenki Dziecięcej
- Wojsko Ludowe – Huta Katowice
- Wystawy
- Zabawy
- Zdjęcia z budowy
- Zdjęcia z wyburzeń
- Zjazdy Absolwentów
- Żniwa
- Życie pod okupacją
- Widoki i panoramy miasta
- Wypoczynek i zieleń
- Zdrowie
- Życie Codzienne
Losowy memoriał
WięcejNasza baza
7576 - skany
175 - wpisy encyklopedyczne
399 - dawne artykuły prasowe